Membrane materials used in MBR technology: polymeric
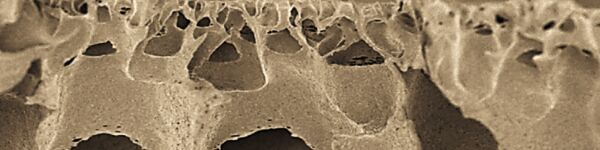
Membrane technology in water and wastewater
A membrane as applied to water and wastewater filtration (i.e. microfiltration and ultrafiltration) is simply a material that allows water and dissolved matter to pass through it while rejecting solid particulate materials. It is ‘perm-selective’, with the degree of selectivity depending largely on the membrane pore size and pore size distribution.
Membranes for filtration are usually fabricated to:
- have a high surface porosity, or % total surface pore cross-sectional area
- have a narrow pore size distribution to provide as high a throughput and selectivity as possible
- be mechanically strong to give structural integrity, and
- be resistant to thermal and chemical attack, that is, extremes of temperature, pH and/or oxidant concentrations that normally arise when the membrane is chemically cleaned.
Specialist membranes are also used for delivering oxygen-rich air into the biological stage of wastewater treatment. This use of membranes, for a membrane-aerated biofilm reactor or MABR, differs significantly from the more established filtration operation of an MBR.
MABRs employ polymeric membranes having the required perm-selectivity for oxygen to allow effective and efficient oxygenation of the biomass in the bioreactor. MBRs employ both polymeric and ceramic membranes, with polymeric membranes being the most established.
MBR membranes are normally fabricated as a relatively thin perm-selective layer (the actual membrane or ‘active layer’) sitting on top of a more open, thicker porous support (or ‘sub-layer’) which provides the necessary mechanical stability.
Polymeric membrane materials for MBRs
A number of polymers have been used to form the active layer of membranes for water and wastewater filtration (Table 1), the latter including MBR technology.
PAN | Polyacrylonitrile |
(HD)PE | (High density) polyethylene |
PES | Polyethersulphone |
PS | Polysulphone |
PTFE | Polytetrafluoroethylene |
PVDF | Polyvinylidine fluoride |
PVA | Polyvinyl alcohol |
A key aspect of membrane filtration of water is membrane surface fouling, i.e. the reduction in permeability caused by constituents (foulants) in the mixed liquor depositing on either the membrane surface or within the membrane pores. Fouling is exacerbated by surface hydrobicity, i.e. ‘water hating’ tendency. Since all polymeric materials are naturally hydrophobic, they must either be surface-modified to make them hydrophilic or, most usually, be 'wetted out' before use. Wetting out defines the process by which water is forced into the membrane pores, normally using surfactants or hydrophilic polymers such as polyethylene glycol (PEG).
The most prevalent polymer amongst the MBR membrane module products offered on the market has been polyvinylidene fluoride, or PVDF. Other less common membrane materials include polyethersulfone (PES) and polyethylene (PE). The combination of good chemical resistance, controllable pore size, and a relatively high mechanical strength, coupled with good flexibility, has meant that the PVDF products have dominated. However, PVDF can be classified as a PFAS (polyfluoroalkyl substance) material and therefore subject to legislative restrictions in its manufacture and use.
Commercial MABR membranes are usually either PVDF or expanded PTFE. Alternative candidate materials include polydimethylsiloxane (or silicone), and polyurethane.
Polymeric membrane configurations
Polymeric MBR membranes are available in all three membrane configurations: flat sheet (FS), hollow fibre (HF) and multitube (MT). MABR membranes are available mainly as hollow fibres.
Two configurations for the HF modules exist (Fig. 1):
- the ‘curtain’ configuration, where the fibres are arranged as a continuous row to form a rectangle, and
- the ‘candle’ configuration, where the fibres are placed in cylindrical bundles.
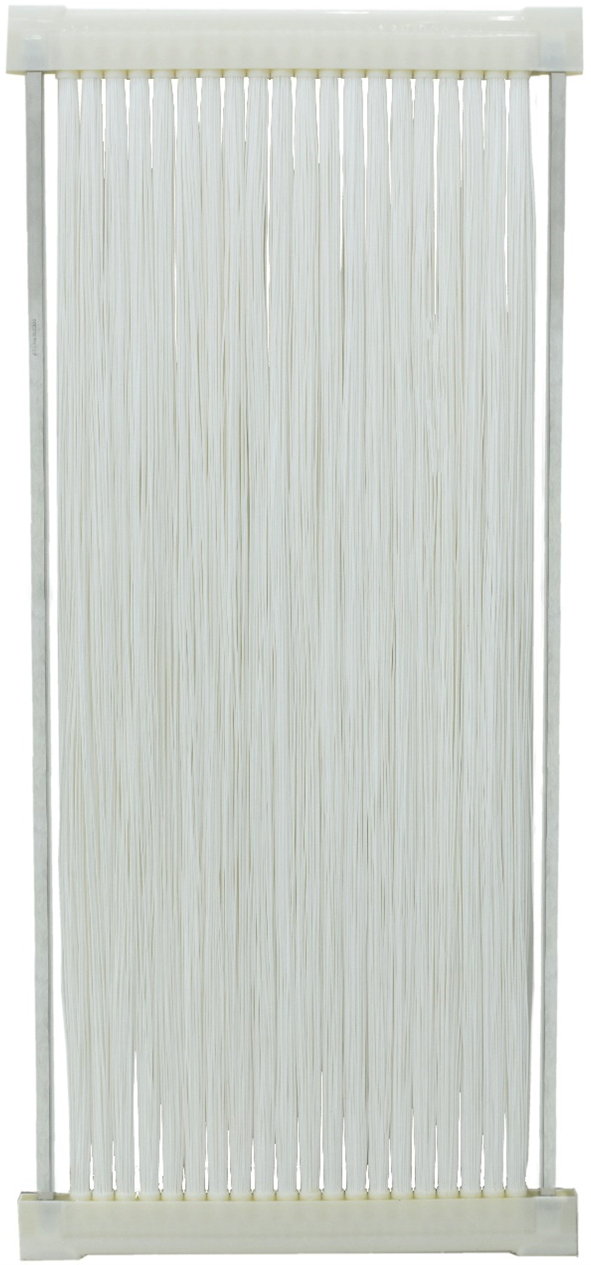
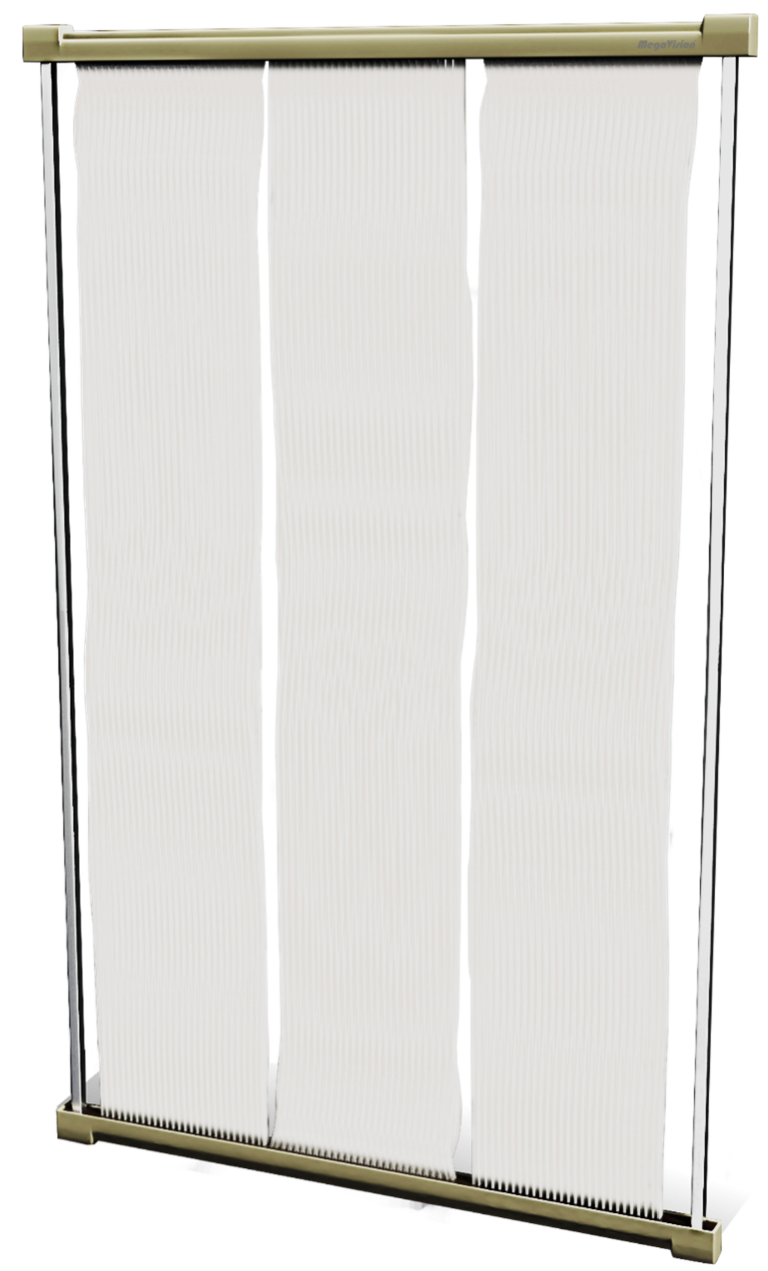
Two membrane module construction variants arise for the FS membrane configuration (Fig. 2):
- the ‘rigid plate’ membrane panel (or ‘cartridge’), where the membrane is attached at its edges to a plastic separator of 3−5 mm thickness, and
- the flexible ‘composite’ membrane, where a single piece of material contains two membrane sheets permanently attached to a central spacer.
The individual rigid plates are placed in a cassette to form a complete module or unit. Composite FS membranes are pre-assembled into the modules. Composite membrane modules can vary in height, with the short modules (where the height is smaller than the length) sometimes being referred to as ‘blocks’.
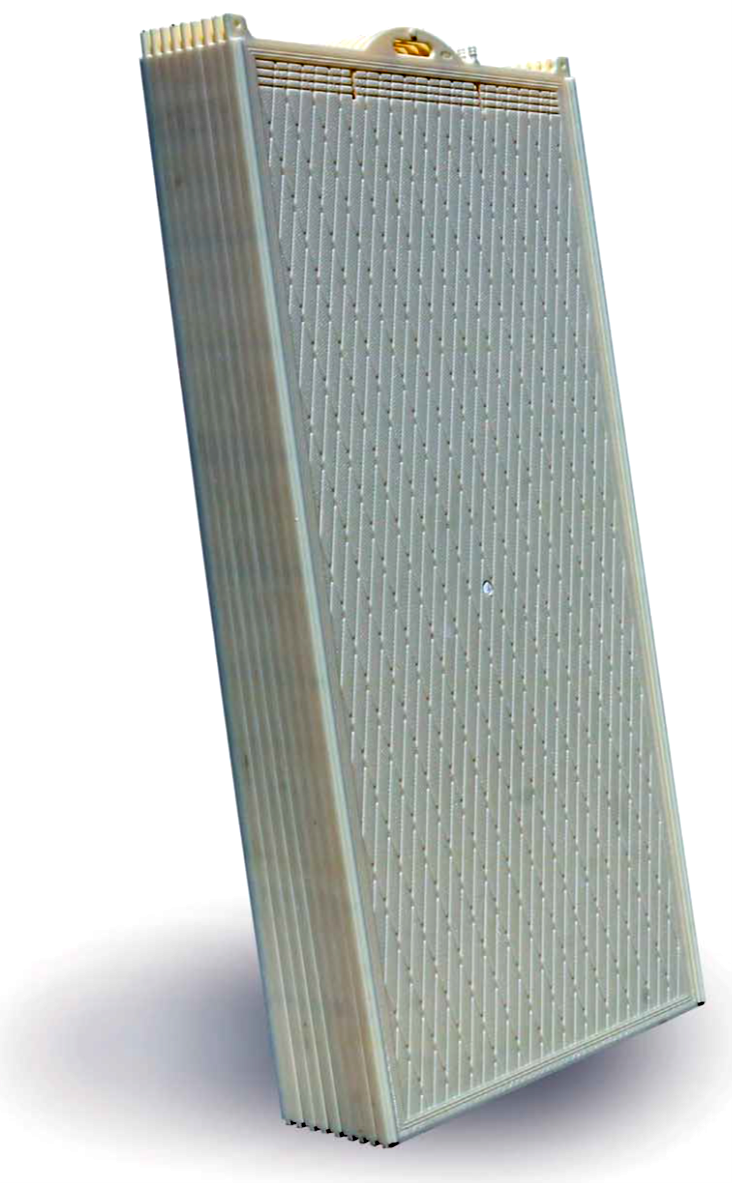
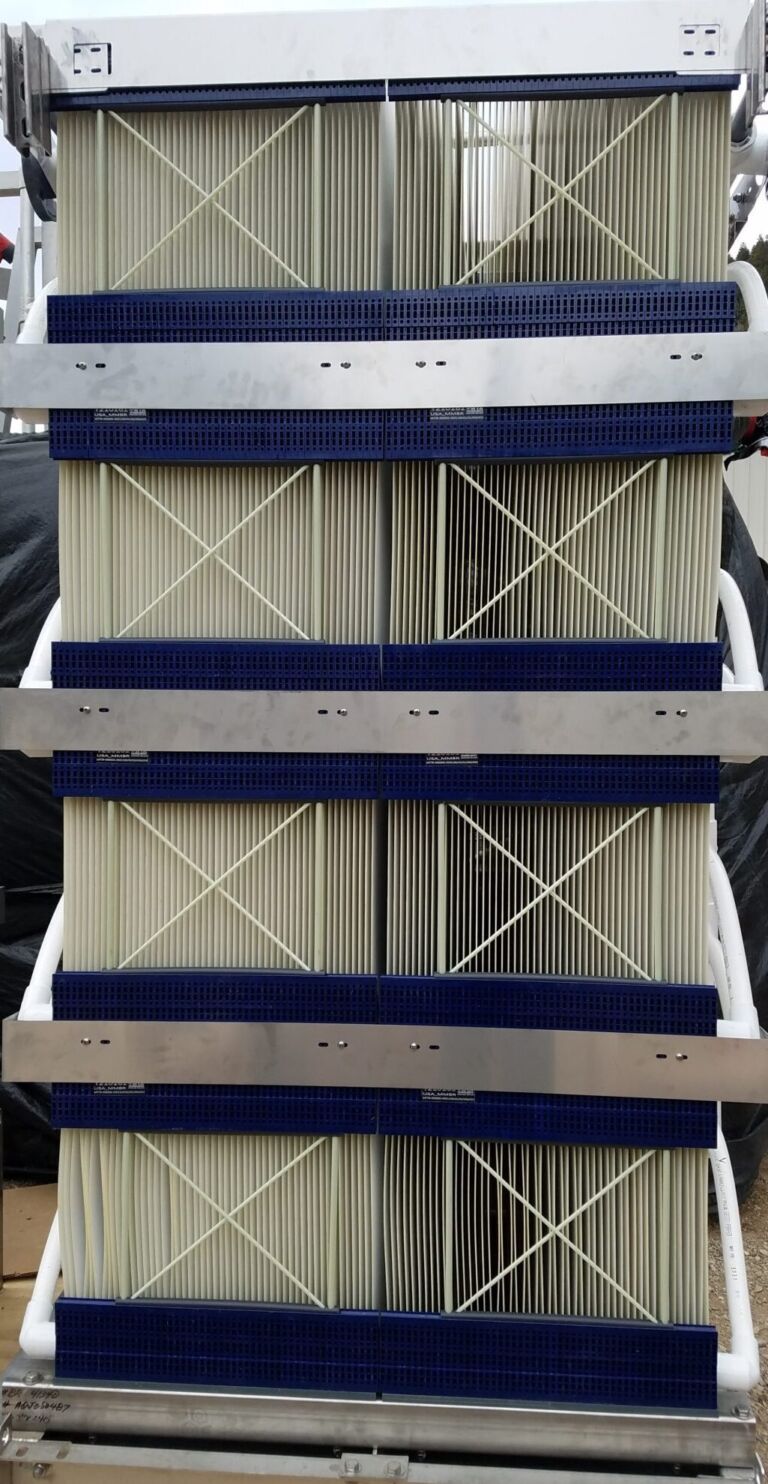
Polymeric membrane manufacture
PVDF membranes are produced by phase inversion from a solution of the polymer in a suitable solvent, such as N-methyl-2-pyrrolidone (NMP) or dimethylacetamide (DMAc). Phase inversion can either be promoted thermally, i.e. by cooling (thermally induced phase separation or TIPS), or by precipitation (or coagulation) using a non-solvent such as water (non-solvent induced phase separation). FS membranes are produced by casting as a thin film prior to phase inversion, whereas HF membranes are produced by extrusion.
The polyolefinic membranes (such as low-density polyethylene, LDPE) are among the lowest in raw production cost of all MBR membrane materials, the pores being generated simply by extruding that material under controlled conditions (or ‘dry spinning’) to produce slit-like pores. This slit-like pore structure is to be distinguished from the more complex thermal induced phase separation (TIPS) process for PVDF, which produces the more classic pseudo one-dimensional pores. The remaining materials − polyacrylonitrile (PAN), polysulphone, polyvinyl alcohol (PVA) and polytetrafluorethane (PTFE) − are much less common.
Polymeric membrane selectivity
Across the entire range of polymers used for water and wastewater filtration, including MBRs, the range of pore sizes is relatively small. Microfiltration (MF) membrane pore size ranges from 0.1 to 0.4 µm, and ultrafiltration (UF) membrane pore sizes are generally between 0.02 and 0.1 µm.
There is little practical evidence to demonstrate any significant difference between the overall rejection capability of the MF and UF membranes. This is largely because, regardless of the membrane pore size, a gel or cake layer forms on the membrane surface during use, and it is this layer which determines the effective membrane pore size.
Polymeric membrane commercial suppliers
Selected established commercial polymeric membrane module suppliers, valid as at March 2023, have been tabulated for the FS and HF configurations. Based on the selection of suppliers listed in these tables those offering PVDF membranes exclusively comprised:
- all but two of the 19 HF module suppliers, and
- 13 of the 17 FS module suppliers.
Whilst the majority of commercially-available MBR membrane modules are polymeric, there is also a small number of suppliers of ceramic membrane MBR modules. Within the municipal water sector ceramic membranes are more extensively used for potable water filtration than in wastewater treatment, and are less commonly employed than polymeric membranes overall.