Energy consumption in MBRs
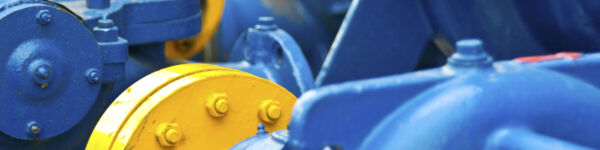
There are a number of components of the energy consumption associated with the operation of an MBR:
- The aeration of the aerobic biological process tank, normally by fine-bubble diffusion (FBD), designed to deliver dissolved oxygen to the heterotrophic bacteria
- The aeration of the immersed membranes for iMBRs, normally by coarse-bubble diffusion (CBD), to scour the membrane surface and keep them clean
- Transfer of the sludge between the membrane and process tanks and elsewhere in the treatment scheme, as demanded by the design
- Pumping of the sludge through the sidestream membrane modules (most often multitube, MT) for sMBRs
- Extraction of the permeate, if membrane permeation is not gravity driven, for iMBRs
- Pumping of the backflush, and heating and pumping of the chemical cleanant, and
- Sundry process control and instrumentation equipment.
As indicated, some of these components are specific to either the immersed or sidestream MBR configuration (i.e. iMBR or sMBR respectively). Process control operations do not generally contribute significantly to the overall energy consumption.
1. Process biology aeration energy demand
Although packages such as Biowin are often used to model biological processes and determine the process energy consumption, it is also possible to use analytical expressions. Most often, for iMBRs, it is two aeration components (#1 and #2) which contribute most significantly to the overall energy consumption. These are expressed as the ‘specific aeration demand’, or SAD.
The base parameters for wastewater treatment by an activated sludge process technology with standard MLE configuration are as follows:
Parameter | Symbol | Units |
---|---|---|
COD removed | ΔSCOD | mg/L |
TKN removed | ΔSTKN | mg/L |
Nitrate generated | ΔSNitrate | mg/L |
COD content of biomass | λCOD | kgCOD/kgMLSS |
TKN content of biomass | λTKN | kgTKN/kgMLSS |
Actual sludge yield | Yobs | kgMLSS/kgCOD |
Density of air | ρA | g air/m3 |
Concentration of oxygen in air | C’A | g O2/g air |
Standard oxygen transfer efficiency per unit depth | SOTE | m-1 |
Depth of aerator in tank | y | m |
Blower energy equation constant (for SI units) | k | - |
Blower inlet pressure | PA,in | Pa |
Blower outlet pressure ~ PA,in + Py | PA,out | Pa |
Hydrostatic head for aerator at depth y | Py | Pa |
Feed flow rate | QF | m3/h |
Process air flow rate | QA,bio | Nm3/h |
Mass transfer correction factor, solids | α | - |
Mass transfer correction factor, salinity | β | - |
Mass transfer correction factor, temperature | γ | - |
The energy consumption can then be determined from the equations for:
a) Oxygen demand from COD and TKN loading in g/m3
O2:
where the values of 1.71 and 2.86 refer to biochemical stoichiometry.
b) Aeration demand from calculated oxygen demand in Nm3
air/m3:
c) The specific aeration energy demand for air pumping (in kWh/Nm3):
The specific energy demand for biological process aeration (EL,bio) in units of kWh/m3 treated water is then given by:
2. Membrane air scour energy demand, iMBR
The membrane air scour is expressed as the specific aeration demand SADm, expressed as the air scour flow QA,mem (in Nm3/h) per unit membrane area A (in m2):
Dividing SADm by the flux J in m/h yields the ratio of the air scour flow to the permeate flow:
The energy demand is then simply SADpmultiplied by specific aeration energy demand for air pumping (in kWh/Nm3), for which the equation given in (c) above can be used with the appropriate value for the aerator hydrostatic head pressure (Py).
3. Liquid and sludge pumping energy
Other fluid pumping energy consumption contributions can be determined based on assumed values for the pumping energy per unit fluid volume and the pumping efficiency. For sludge transfer between the membrane and process tank, the energy consumption is also proportional to the recycle ratio: the ratio of the membrane:process tank recycle rate to the permeate flow rate.