Industrial MBRs − petroleum sector
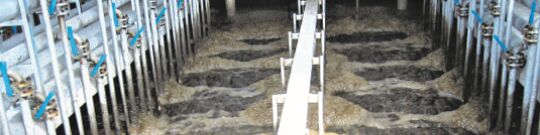
Membrane bioreactors in the petroleum sector
The petroleum industry comprises three elements:
- exploration,
- refining, and
- petrochemical
where refining and petrochemical production may be combined. Exploration concerns the abstraction of mineral oil and gases from underground reservoirs, which generates produced water (PW) as the main effluent. Refining mainly concerns the separation of the crude oil into useful fractions, and petrochemical operations are those involving chemical modification of these fractions into further products.
It is only in the latter two areas that MBRs have been implemented, the largest industrial MBRs installed worldwide being associated with refining.
Treating refinery wastewater
Refinery wastewater quality varies significantly according to the process cycles. Its treatment is generally based on classical activated sludge treatment, usually with an initial flotation sequence to remove the oil.
The simplest flotation device is the American Petroleum Institute (API) separator, the 'workhorse' in any refinery for the separation of oil/water and solids, which allows both settlable solids and large oil droplets (>150 µm) to be removed by up to 90%. This primary step is then often followed by clarification. This may comprise corrugated plate separators preceded by coagulation/flocculation and followed by either dissolved air flotation (DAF) or induced gas/air flotation (IGF/IAF). These technologies target much smaller oil droplets − 10-25 µm − and reduce the suspended oil concentration to around 25−50 µm.
Flotation, along with the increasingly employed electro-coagulation process, is most effective (in terms of % removal) for high suspended oil concentrations, such as those arising in the desalter effluent. Such effluents, along with the spent caustic, also have a considerably higher salt content than the remaining effluent streams.
It is therefore desirable to treat these three streams separately from the remaining low-TDS streams to allow both pre-treatment for oil removal and segregated biological treatment of high-TDS effluent. Since segregation is rarely employed, significant shock loads arise in refinery effluents from dissolved salt and oil, in particular from sub-optimal electrical coalescence (grid technology) or intermittent discharge of the mud wash from the desalter.
Biological treatment
While biological treatment of PW is still at the developmental stage, it is routinely employed for refinery and petrochemical effluents where MBRs have been implemented.
Published data indicate organic contaminant removals, expressed as chemical oxygen demand (COD), generally in the range 84−99%, with fully optimised systems achieving >95% COD removal as well as complete nitrification.
Reported results indicate COD removals to vary little with the hydraulic retention time, but strongly dependent on the feed water composition and, in the case of nitrification, pH: a decrease in pH levels to below 5.8 has been shown to reduce nitrification to as low as 80%. Biotreatment may also be enhanced by the addition of powdered activated carbon to the bioreactor, which helps retain the dissolved organic matter and thus extend the treatment time.
While biological treatment is the most common and cost effective method for organics removal employed at oil refineries, the required treated water may be challenged by both nitrification inhibition and by the biorefractory nature of the organic fraction. A loss of nitrification can arise both from a C:N imbalance or from toxicity. In such cases where biological treatment is challenged, advanced oxidation may be necessary and its implementation within the sector is becoming increasingly common.
Petrochemical effluents
Petrochemical effluents tend to be less challenging than refinery effluents, due to their reduced recalcitrance and water quality fluctuation. An exception is effluents containing PVA (polyvinyl alcohol) from PVC (polyvinyl chloride) manufacture. These are relatively resistant to biodegradation and so require a high MLVSS concentration and long treatment times. This makes such effluents very conducive to treatment by MBR technology, particularly where spatial restrictions exist.