Membrane permeation costs
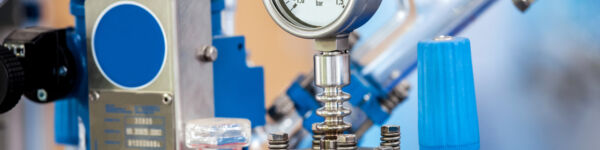
Membrane permeation costs
Costs associated with the pumping of water through the membrane relate to the transmembrane pressure (TMP), the flux and the operating protocol. The associated energy demand tends to be lower than that for aeration or sludge transfer.
Since all membrane processes demand downtime for cleaning, and may also use some of the product permeate water for this function, the net flux (see Key parameters − membrane side) is always lower than the instantaneous flux − normally by somewhere between 5 and 15%. The actual energy demanded for permeate pumping can range from almost negligible, for a flat sheet (FS) membrane in an immersed technology (iMBR) where permeation is gravitationally-driven by a head of less than 2 m, to the second most significant contribution to SED (after process aeration) for a sidestream process (sMBR) treating a challenging industrial effluent.
For ‘classical’ pumped sMBRs, which are predominantly based on the multitube (MT) membrane configuration, pumping at a significant crossflow (of 2−4 m/s) through tubes of around 6−8 mm in internal diameter and at TMPs of 2−5 bar is required to sustain relatively high fluxes (compared with iMBRs) for long periods of time between chemical cleaning of the membrane.
For an immersed hollow fibre (HF), which operates under permeate suction, the TMP is generally between 0.15 and 0.35 bar − somewhat higher than an FS but much lower than the sMBRs.
Lastly, there is also the air-lift sMBR, which works on a similar principle to the FS iMBR in that the air is used to lift the sludge through the membrane. In this case, however, the membrane is generally MT in configuration, vertically oriented and placed outside the tank. A combination of sludge pumping and air scouring is used to achieve overall SEDm values comparable to those achieved in iMBRs.