Industrial MBRs − food and beverage sector
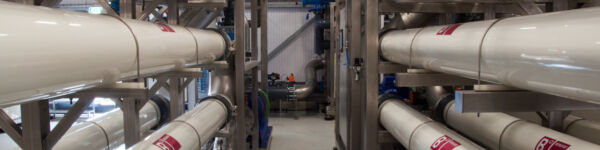
Membrane bioreactors in the food and beverage sector
The food and beverage (F&B) sector produces both finished products for consumption and intermediate products destined for further processing.
The sector is diverse and includes dairy, maltings, breweries, distilleries, wineries, soft drinks, cereals, potato chips, salads and produce, coffee, confectionery, edible oils, meat and poultry processing and various other prepared foods.
The sector is heavily reliant on good quality water, which is the principal ingredient in all beverages and a number of foods. However, most water is used for ancillary processes including washing, cooling, heating, cooking and conveying, plus cleaning and sanitising of equipment and to provide site utilities.
Food and beverage effluent characteristics
Effluent generated in the F&B industry is typically high in organic loading, with BOD and COD concentrations that can be 5−100 times higher than for domestic wastewater.
The TSS also varies from negligible to very high concentrations, and may contain FOG (fats, oils and grease), e.g. from meat, fish, dairy and vegetable oil production. They may also contain high levels of ammonia and/or phosphorus if large quantities of phosphoric acid are used in the process, such as for vegetable oil de-gumming or cleaning operations. Equally, some F&B wastewater can be deficient in N and P and require nutrient balancing. However, they are generally readily biodegradable with COD/BOD ratios ranging from ~0.4−0.5 for bakery products to >0.8 for poultry processing.
Membranes use in the food and beverage sector
Membranes use in the F&B industry predates MBRs, having been used for process waters rather than effluent treatment. The implementation of membranes and in particular MBR technology for industrial effluent treatment has only occurred since the mid−late 1990s. Market penetration has followed the same pattern as for municipal wastewater for much the same reasons − declining MBR costs, increasing freshwater supply costs, increasingly stringent legislation, improved technology design and reliability, and spatial restrictions, among others.
Examples of iFS industrial effluent applications in Japan date back to the mid 1990s. Early examples of sMBR technology applications in Europe include an 800 m3/d dairy in France, based on ceramic membranes from Degremont which was commissioned in 1997, along with the Orelis ‘plate and frame’ MBR for a 50−120 m3/d dairy wastewater. MBR technology applications have now extended across almost all sectors of the F&B industry and are widely considered to be the best treatment solutions, especially if water reuse is a requirement.
Key motivations for MBR technology implementation in the sector have been:
- water recovery and reuse, motivated primarily by cost savings
- water scarcity (and regulatory requirements relating to water conservation)
- security supply, and
- strategic corporate planning.
Key issues surrounding the water recycling in the sector concern the maintenance of hygiene and food safety standards using effective control measures. Since effluent reuse plants based on the two-stage MBR−RO within the sector have been established since the early noughties, the initial reticence associated with water recycling has now largely been replaced with widespread acceptance. A final disinfection stage (chemical and/or UV) is normally sufficient to meet the required strict quality assurances for treated water reuse in the F&B sector.