Membranes for polishing biologically-treated wastewater
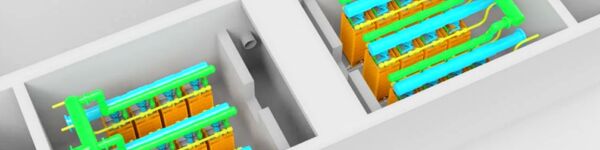
Wastewater polishing and reuse with membranes
Prior to the development of MBR technology, clarification and substantial disinfection of wastewater was achieved by employing microfiltration (MF) or, most often, ultrafiltration (UF) downstream of a classical activated sludge (CAS) process. This ‘non-integrated’ application of membrane technology following biological treatment is usually referred to as 'polishing'.
Membrane polishing of wastewater is widely used in water reuse applications. It is often preferred over MBR technology (i.e. 'integrated' membrane separation) since the membrane component can simply be placed downstream of the secondary clarifier with no further modification of the existing infrastructure.
Dwindling freshwater resources globally has led to an increasing number of wastewater reuse schemes, particularly in arid regions.
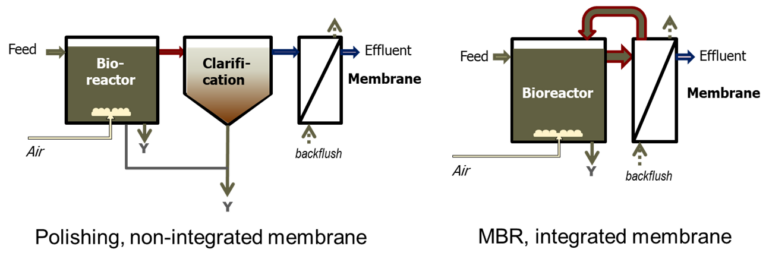
There are three types of water reuse applications, where wastewater is recovered and reused for some purpose:
- Non-potable reuse (NPR), where the recovered water is used for some purpose other than potable supply (e.g. irrigation, industrial process water, etc)
- Indirect potable reuse (IPR), where the recovered water passes through an ‘environmental buffer’ before being used as a supply of potable water, and
- Direct potable reuse (DPR), where the recovered water is used as a potable water supply without passing through an environmental buffer.
IPR and DPR systems employ municipal wastewater as the feed, and are subject to very high treated water quality standards. NPR can either be based on industrial effluents, where the product water is most often reused on site, or municipal wastewater.
Membrane materials and configurations for wastewater polishing
Membrane modules used for polishing have historically been the same type as those employed in potable and pure water filtration. These membranes are most often polymeric, cylindrical in geometry (i.e. filaments), and normally between 0.5 and 2 mm in outside diameter. Flow through cylindrical membranes can either be out-to-in, or 'shell-side to lumen-side', as with a hollow fibre (HF), or in-to-out ('lumen-side to shell-side'). In-to-out flow through a filament is representative of the 'capillary tube' (CT) configuration, but CT modules are often referred to as 'hollow fibre' by the suppliers.
The implementation of ceramic membranes for both potable water treatment and for polishing has become more widespread. Ceramic membrane modules may be either multitubular (MT) or flat sheet (FS) in configuration, and may formed from a number of different ceramic materials (alumina, silica, silicon carbide, titanium oxide or zirconium oxide)
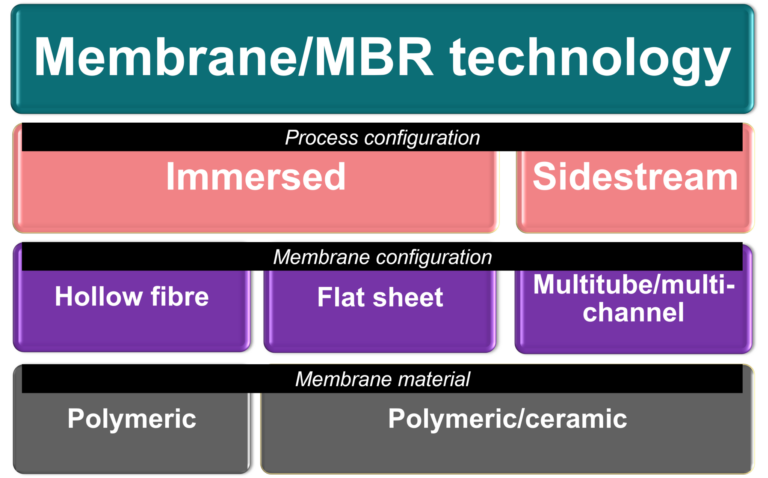
Membranes used for polishing can be immersed in a tank and operated under suction, like those used in immersed MBRs (though not necessarily requiring air scouring), or skid-mounted and water delivered to the membrane under pressure (or 'pumped'). For the most widely used membrane configuration in wastewater polishing, HF, the modules are usually skid-mounted - as with the sidestream MBR membrane modules.
For polishing applications, the solids concentration and loading onto the membrane is considerably lower than for an MBR membrane: <50 mg/L compared with 8–12 g/L for the MBR. Consequently, the membranes can be much more tightly packed in the module. Volumetric packing densities may exceed 2000 m2 membrane area per m3 internal module volume, compared with generally less than ten times this packing density for the iHF MBR modules. The lower solids loading also permits higher fluxes, particularly for the ceramic membranes, demanding a smaller membrane area.