Pretreatment: Screening and degritting
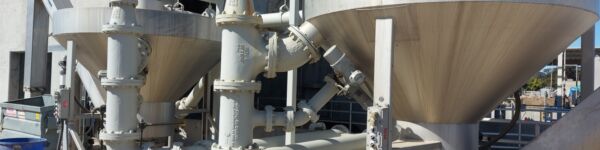
Screening
Screens are placed at the inlet works (coarse screens) and downstream of the degritter and/or upstream of the biological and membrane tanks (fine screen) for removing extraneous rag-like material by sieving. They are essential for suppressing the clogging of membrane channels with gross solids in the influent which can otherwise agglomerate around the internal infrastructure of the downstream process and membrane tanks.
Screens are supplied in a number of different configurations according to the precise application. The most common screen designs are:
- spiral-screw gravity-flow stationary screens
- through-flow, escalator/step screens
- pumped-flow rotational drum screens
- gravity-flow rotational drum screens
- centre-flow and dual-flow band screens
- single-entry, double-entry and duet drum screens.
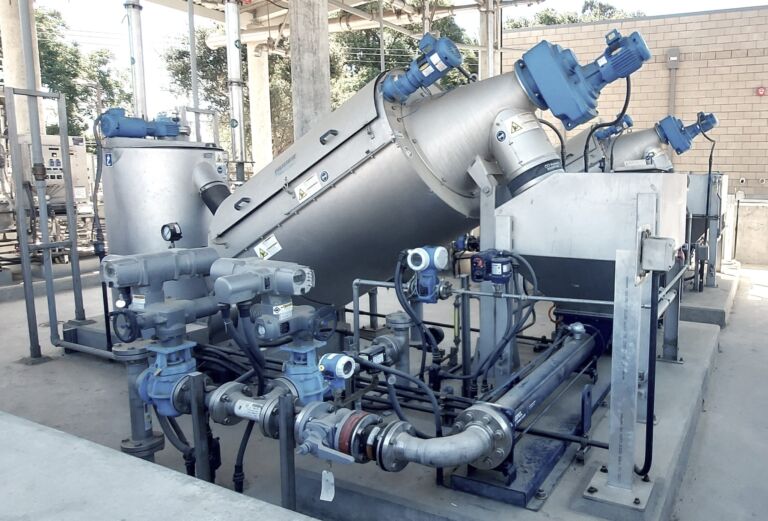
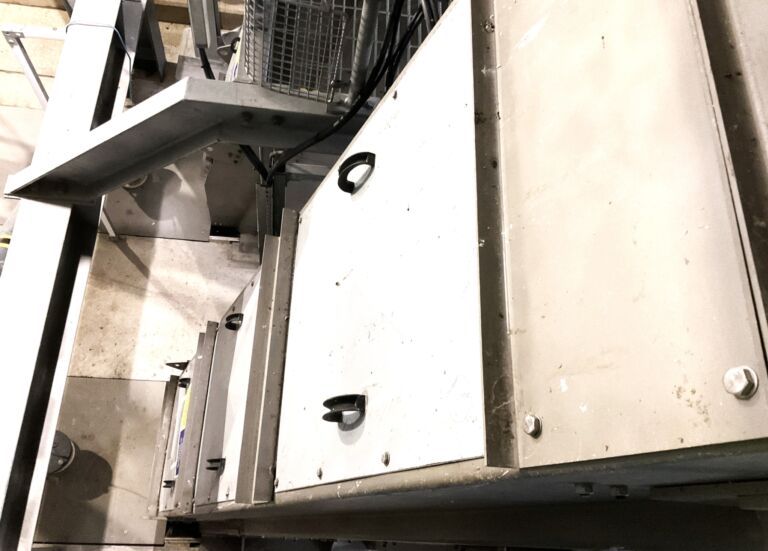
Two key design parameters concerning the screen itself are:
- the rated size of the aperture, and
- the aperture shape.
Apertures can either be circular (or ‘1D’, one-dimensional) or rectangular (‘2D’) in shape. The rating of rectangular-apertured screens (referred to as ‘bar’ or ‘slot’ screens, and sometimes constructed of ‘wedgewire’) is given by the narrowest dimension of the rectangle. Practical experience has revealed 1D screens of the same rating as 2D ones to be more effective protecting the downstream membranes, but generate larger amounts of screenings and create larger headlosses than the 2D screens.
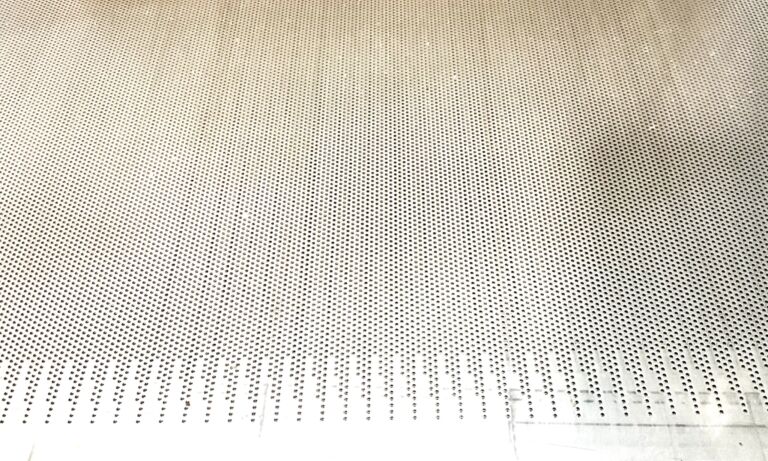
Coarse screens at the inlet works are normally rated at 6 mm, and the apertures are normally slits for this duty. Fine screens for protecting the membrane can be rated between 0.8 and 2 mm, depending on the membrane type, and can have slit, square or circular apertures. Large municipal MBR plants may have an additional coarse screen immediately upstream of the degritter to reduce the load on the fine screen.
As with membranes, screens have a flow capacity which roughly relates to the aperture size. Screens are kept clean by various means, including the use of water sprays, brushes and agitation of the screen (most simply by rotation). The effectiveness of the cleaning then affects the flow capacity. The velocity through the screen – analogous to the flux through the membrane – is the key design parameter and, as with the membrane itself, there is little financial justification for under-specifying the screen on this basis given the potential impact on operational costs.
Finally, besides the velocity, a key performance parameter of a screen is the screening capture ratio (SCR). A properly-sized 2 mm screen will remove 94−96% of all pseudo-spherical particulate screenings, whereas a 1-mm screen will remove up to 98.7% of all filamentous particulate screenings such as human hair, cotton and wood fibre. Filamentous debris can pass readily through a 3-mm and 2-mm fine-screen aperture, as well as 2-mm and 1-mm slotted screens, if they approach the screen orthogonally (i.e. end first).
Appropriate selection and sizing, along with proper maintenance, of the screen is of critical importance in sustaining operation of the plant. This includes the selection and O&M of the primary coarse screen and grit removal technology, since this reduces the load on the fine screen and thus protects both the fine screen and the downstream membrane.
Comminutors (also called 'macerators' or 'grinders') are sometimes installed upstream of screens to reduce the load of coarse particles on them. However, this is known to lead to operational problems for MBRs since the fibres which have passed through the screens can agglomerate to form long rags in the membrane tank (Stefanski et al, 2011), necessitating an onerous manual external mechanical clean.
Degritting
Grit in wastewater takes the form of inorganic solid particles in the 0.2−4 mm size range of density predominantly above 1800 kg/m3. Degritters are intended to selectively remove solids, which may otherwise impair downstream processes through abrasion (of mechanical equipment or concrete channels) or accumulation, most typically in anaerobic digesters (ADs) or aeration lanes which then reduces the time between their scheduled maintenance. The cost of these impacts has been estimated as being around $8 per megalitre of water treated (Judd et al, 2017).
The standard performance criteria used for the degritter technology is 95% removal of such solids above 210 μm in size, based on national standards (USEPA, 2003). However:
- a) practitioner accounts and experiences (Sherony and Herrick, 2015; Flanagan, 2014; McNamara et al, 2013, 2012) suggest that grit entrainment imposes a challenge even for degritters apparently meeting the specification, and
- b) the combination of grit with fats, oils and grease (FOG) tends to reduce the net granule density (Judd et al, 2017).
Up to 30% of the total grit content has been determined as being less than 200 µm in size with a significant fraction below 150 µm (Flanagan, 2014). The combination of grit with FOG tends to make them more buoyant. FOG can make up almost half of the total grit volume (Judd et al, 2017).
Degritters can be configured as tanks, channels or cyclones. The most common degritters are simple gravitation tanks, called ‘detritors’, which allow the heavy grit particles to sink to the tank base through employing an appropriately low surface overflow rate. Angled scrapers then gather the grit together and direct it to a collection chamber.
In aerated grit chambers the grit is passed along a channel with a V-shaped base. Air introduced to the channel exerts a helical motion on the grit particles passing along the channel length. This agitation washes the grit, providing separation of the attached FOG, whilst allowing settlement of the grit.
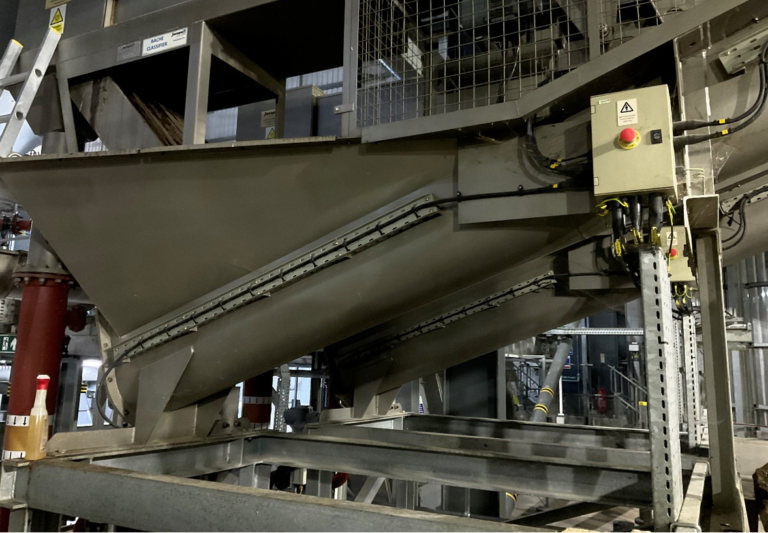
Cyclonic or vortex degritters add a centrifugal component to the gravitational separation, increasing the separation efficiency for a given tank size.
For large MBR-based municipal WwTPs degritters are placed downstream of the coarse screen and upstream of the fine screen stage. They are often fitted with classifiers to wash collected grit ready for reuse – normally in the construction industry.