Industrial MBRs − textiles sector
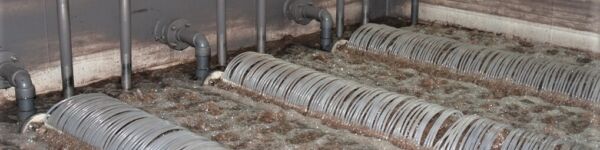
Membrane bioreactors in the textiles sector
Textiles can be classified according to the origin of the material:
- cellulose fibres from plant sources (such as cotton, rayon, linen, ramie, hemp and lyocell)
- protein fibres from animal coats (wool, angora, mohair, cashmere and silk), and
- synthetic fibres from polyester, nylon, spandex, acetate, acrylic and polypropylene.
Most textiles are produced from cotton liners, petrochemicals and wood pulp. As with many other industrial sectors, the textile industry consumes large amounts of water: about 80−150 L per 1 kg of fabric. The sector encompasses a large number of different textile processing operations and generates effluents of widely different characteristics with respect to specific pollutants and aggregate water quality determinants such as BOD, and TS. Effluents differ in their biodegradability, toxicity, FOG content and, most notably, colour.
Almost all dye processes leave residual colour in the effluent, the proportion of unfixed dye varying between almost negligible amounts for pigments to close to 50% for reactive dyes. This is problematic due to their high resistance to biodegradation (with most CAS plants removing no more than 50% synthetic colour) combined with the intensivity of the colour.
The strong colour imparted by most dyes demands removal to very low concentrations prior to discharge for consents based on colour. While insoluble dyes, such as indigo used for denim, can be physically removed by a microporous membrane, biorefractory soluble dyes are only rejected by dense membranes (RO or possibly NF).
MBRs in textiles wastewater treatment
MBRs allow more intensive biological treatment over that attained with CAS through extending the SRT, although downstream treatment appears to be necessary if the required product water quality is based on colour.
Evidence from MBR pilot studies suggests that, while the COD removal from textile effluents can exceed 90%, removal of soluble colour does not often exceed ~75%. Removal is highly variable and dependent on the condition of the sludge, since the biorefractory nature of the dyes means that the main removal mechanism is adsorption. This is analogous to the reported behaviour of pharmaceutical and personal care products and metals, where residual metals levels in the treated water of the MBR are roughly half that of the CAS.
The MBR does, however, offer a clear advantage over a CAS when reuse is the end objective. A number of full-scale examples of MBR technology applied to wastewater reuse at textile mills indicates the use of downstream RO to remove the residual colour. The MBR provides an effluent of low SDI suitable for downstream purification by RO or NF with no further treatment required other than cartridge filtration.