Immersed hollow fibre MBR membranes: a summary of commercial products
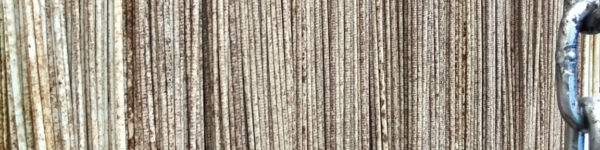
Simon Judd
In this second of three features exploring the MBR membrane market, Simon Judd summarises characteristics of some of the commercially-available immersed hollow fiber membranes for wastewater treatment.
Simon is a Director of Judd Water & Wastewater Consultants, and co-owner of The MBR Site and SludgeProcessing.com.
1. The original iHF products
Immersed hollow fibre (iHF) MBR membranes were first commercialised in 1992 by Mitsubishi Rayon in Japan. The module was based on horizontally-oriented fibres of low-density polyethylene (LDPE), and was implemented in Japan at that time.
A year later the first polyvinylidene fluoride (PVDF) membrane (Zeeweed) was introduced by the Canadian company Zenon. This product remains the most commercially significant iHF product today, having been implemented globally with an associated treatment capacity running to several gigalitres per day. In 2006 Zenon was acquired by GE, and GE’s Water and Process Technologies group was then subsequently bought by Suez in 2017. Suez recently became part of Veolia.
The ZeeWeed HF forms the basis of the ZW500 membrane module series (currently ZW500D) for MBRs. It employs a 1.9 mm outer diameter (OD), 40 nm pore PVDF membrane material attached to a woven reinforcing braid to provide mechanical strength, as in the example of a braided core fibre shown in Fig. 1a. The fibres are potted at both ends, i.e. with two headers, and the module is rectangular in shape. The modules are fitted into a cassette to form a cuboid stack.
Whilst there have been a number of modifications to the original ZeeWeed module from the early 1990s, the basic features have not changed greatly. The key elements of the design of the module are reflected in those of many other iHF products which have since entered the market (Fig. 1b).
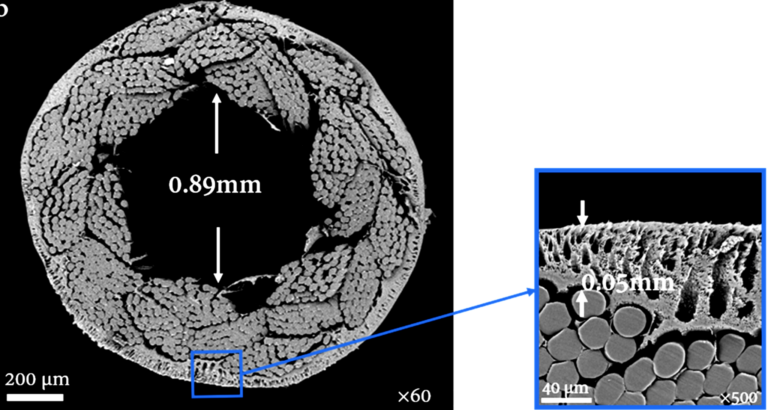
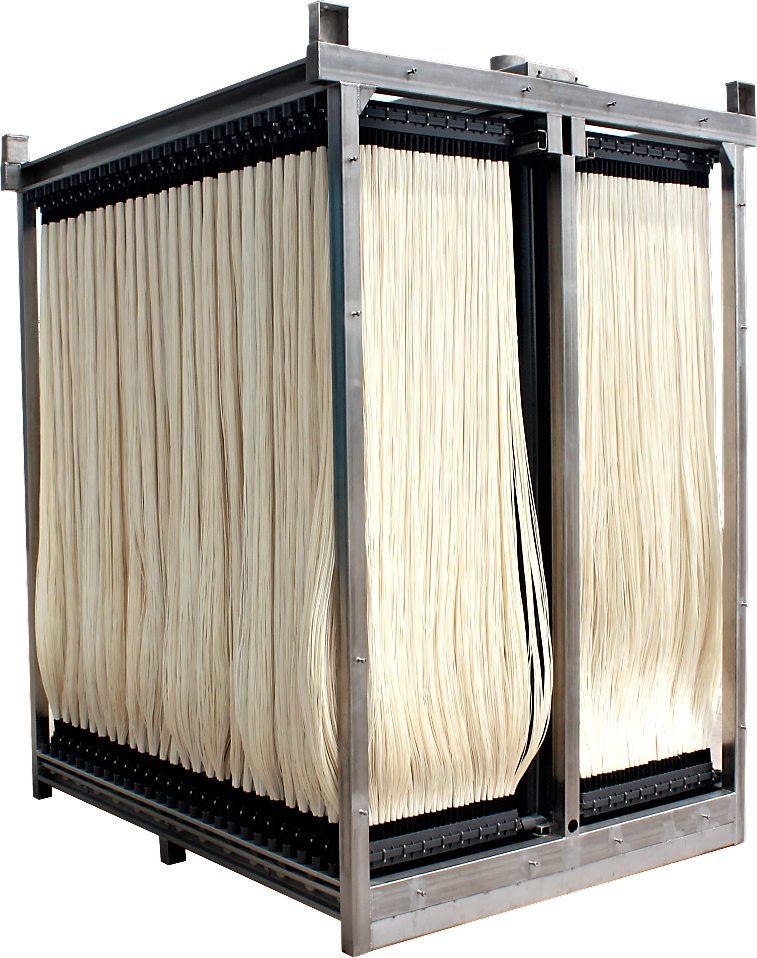
2. Commercial product features
There are probably more than 40 iHF module products, including hybrid configurations which combine the features of flat sheets and hollow fibres, available from different suppliers across the world. The precise number is difficult to estimate. A substantial number of these are offered by Chinese suppliers to satisfy the very large wastewater treatment market in the country. These companies and their products are mostly not identifiable using the usual search engines.
Most of the commercially-available iHF module products specifically identified in this article (Table 1) have a number common characteristics:
- All the listed products use vertically aligned HF fibres of, predominantly, 1.9−2.8 mm external diameter.
- The membrane material used is PVDF for all but three of the 22 products listed in Table 1, the exceptions being:
- the Poreflon product of Sumitomo (Japan), which is based on polytetrafluoroethylene (PTFE)
- one of the two products offered by Econity (Korea), which uses LDPE, and
- the C-Mem product by SFC Umwelttechnik (Austria), which is high-density PE (HDPE).
- PVDF filaments of 2 mm diameter or more are usually fitted with a braided core (Fig. 1a) composed of a woven textile braid of high tensile strength.
- Almost all of the membrane modules have two headers, two exceptions being the Koch products and the Membion for which the fibres are potted only at the base and are sealed individually at the top.
- The geometry of the modules is rectangular, with a length between 0.53 and 1.25 m, a thickness of 30−92 mm and a height of 1.6−2.4 m in all but a few cases. The exceptions to this geometry are:
- the DuPont Mempulse, Sumitomo Poreflon, and Membion (the latter shown in Fig. 2) products, which all have a square cross-section and comprise a small number (<10) of very narrow rectangular elements
- the Econity product range which, uniquely for an iHF-configured MBR technology, is based on stackable blocks (Fig. 3), and
- the SFC Umwelttechnik C-MEM module, which is a cylindrical cartridge.
The C-Mem and the Membion products have both been introduced within the past 2−3 years. They employ relatively small modules within their own discrete housing (Fig. 2); the housing presumably helps retain the flow of air bubbles within the vicinity of the fibre.
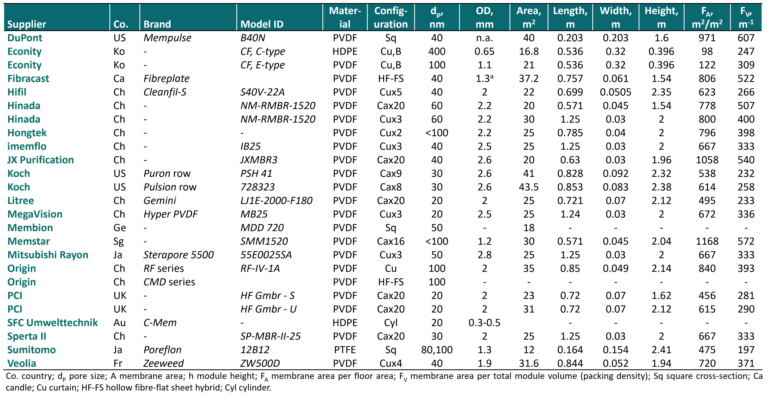
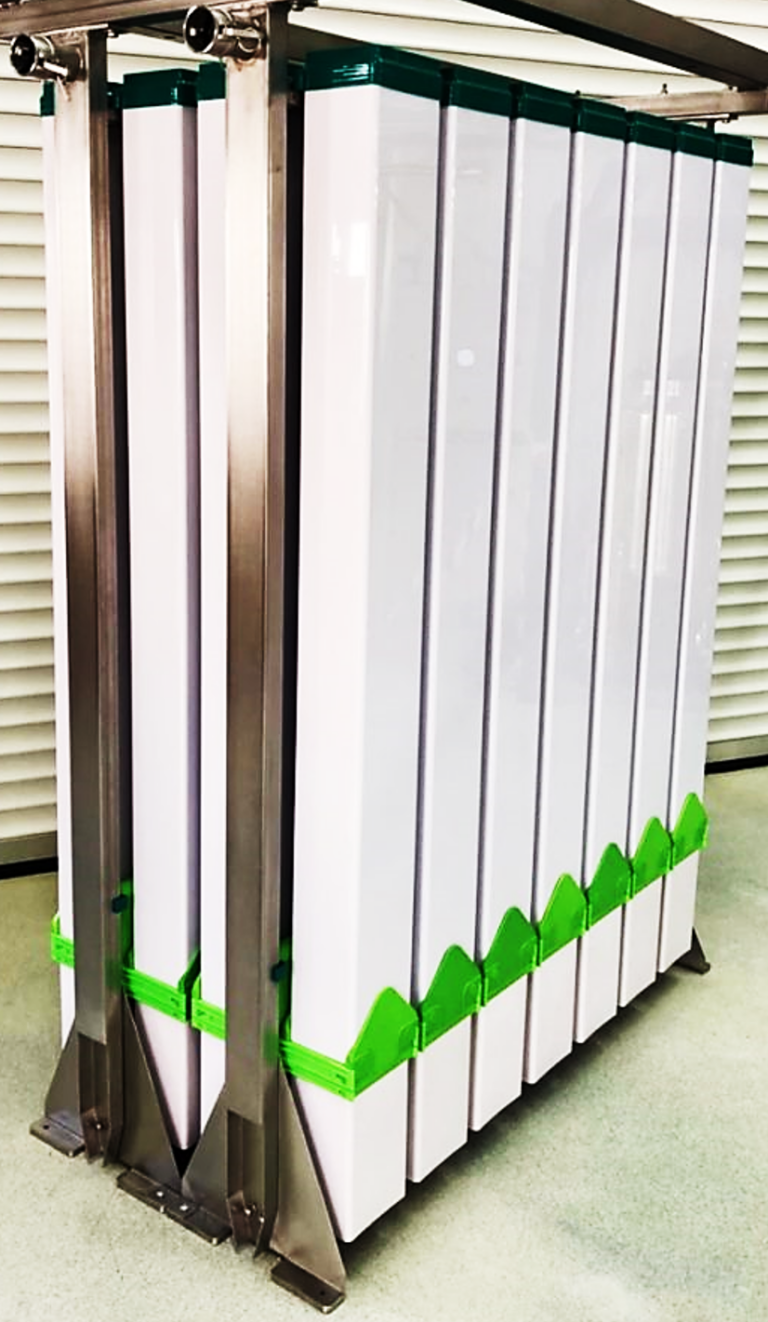
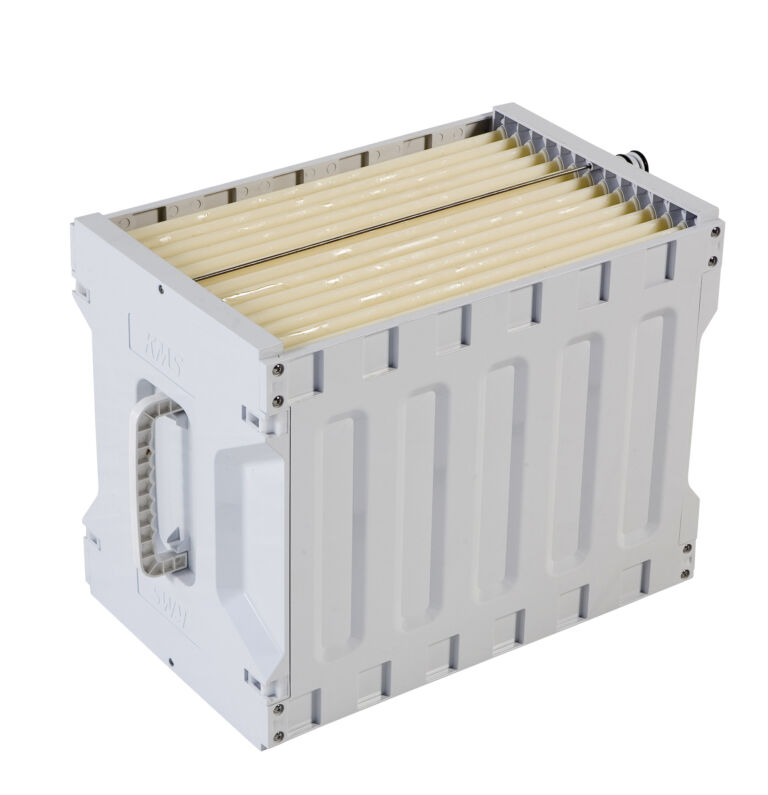
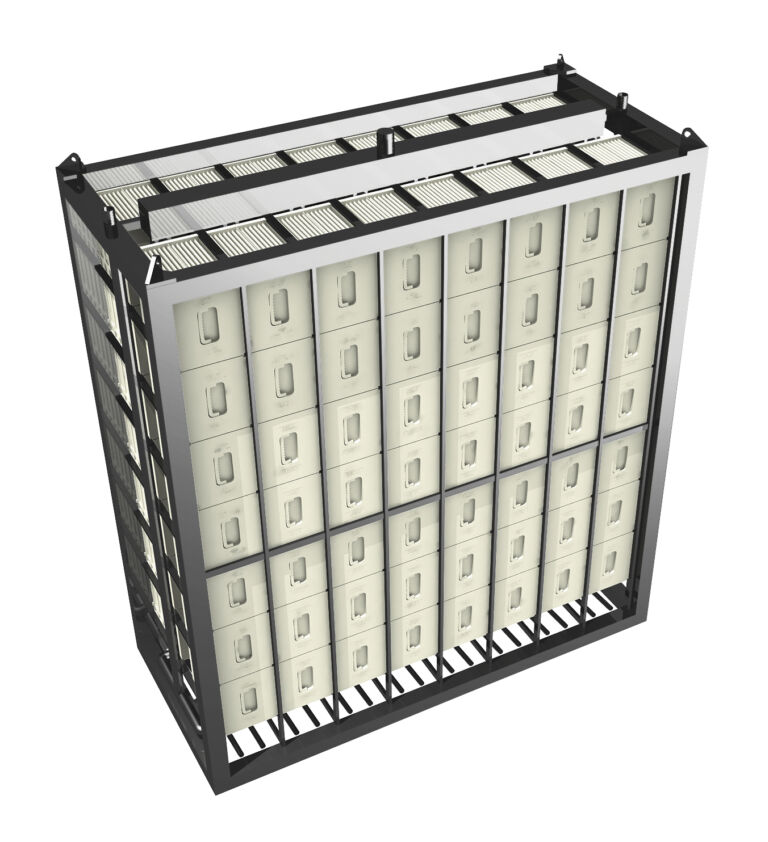
There appear to be two configurations for the standard rectangular geometry modules:
- a) a row cylindrical bundles, or
- b) a series of rectangular bundles.
Cylindrical bundles are often referred to as 'candles', whereas a continuous row of fibres forming a rectangle is usually termed a 'curtain'. Five of the suppliers listed in Table 1 appear to offer products based on a row of 20 candles (Fig. 4a), denoted 'Cax20' in Table 1. Four are based on a row of three curtains ('Cux3' in Table 1) within a 1.25 m-long, 30 mm-thick module (Fig 4b). The Koch modules are described as 'rows', comprising as they do a row of 8−9 candles each with an integral aerator within the fibre bundle.
Other Chinese companies supplying HF module products include CNK Hong, Hinada, Hongtek, Jianhua, Membrane Solutions, Microna, Morui, Motimo, Nollet, Sujing, Suntar and Zhaojin Motian. These products all appear to be rectangular modules fitted with PVDF membranes.
The US company Evoqua offer containerised MBR systems (the Xpress product range), based on the former Memcor membrane. The Memcor membrane otherwise forms the basis of MBR products offered by DuPont, who acquired the membrane business from Evoqua in 2019.
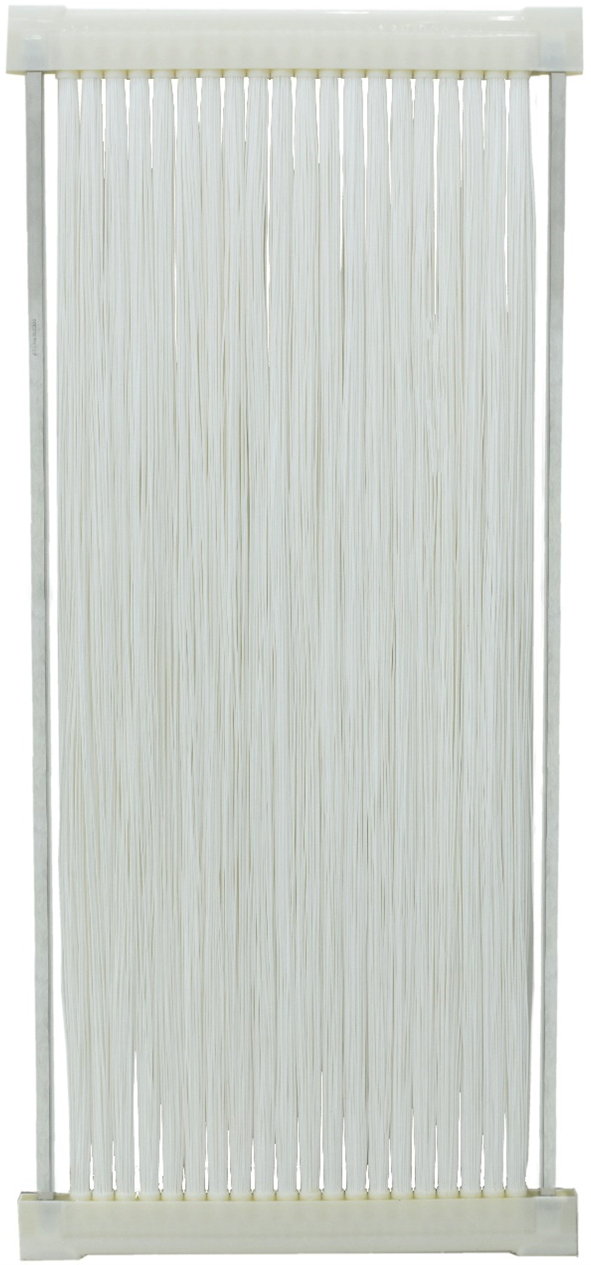
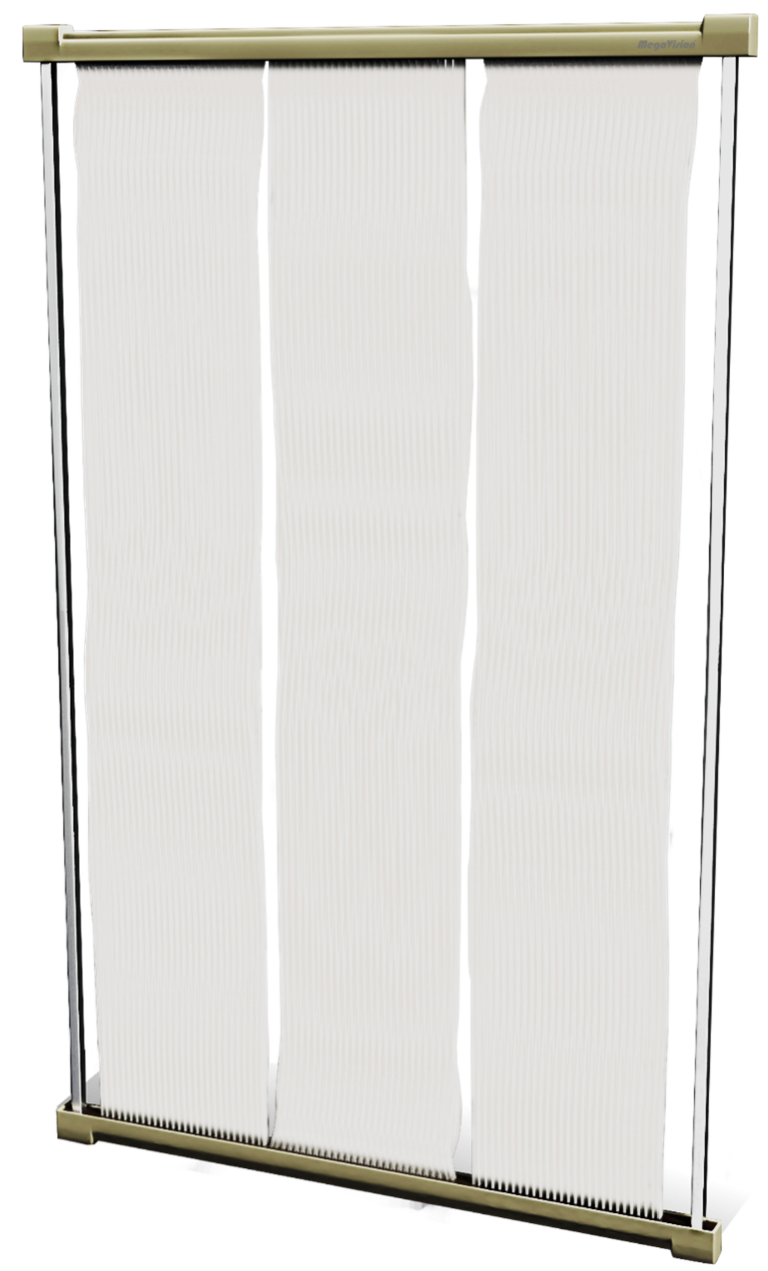
Aside from the iHF products based on vertically-aligned fibres, there are also two products which can be considered as being conjoined horizontal hollow fibres: the Fibreplate by the Canadian company Fibracast and the CMD product range from OriginWater in Beijing. OriginWater are the leading supplier in China – and possibly the world – in terms of the installed treatment capacity. They introduced their 'corrugated' membrane (Fig. 5) in 2021; Fibracast were formed in 2010 and brought their product to market at around that time. In both cases the membrane can be defined as a flat sheet but displays characteristics, most specifically the packing density, more akin to a hollow fibre.

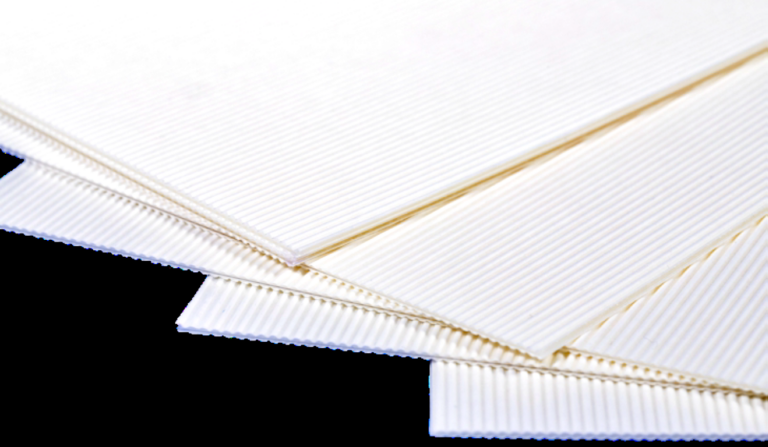
3. Membrane air scour
As with the immersed flat sheet module, a key component of the iHF technology is the air scouring of the membrane. In this regard, the aerator can either be integrated with the cassette or frame within which the modules sit or be fitted to the individual modules.
For the majority of the products listed the aerator is fitted to the frame. For a few of the products, specifically the Veolia ZW500 LEAP module, the DuPont MemPulse, the Koch Pulsion, the Litree ZenMBR, and the Membion, the modules are individually fitted with dedicated aerators. In such cases the aerator is designed to intermittently deliver a very large 'slug' of air, lasting perhaps only 2−4 seconds over a 12−15 second cycle. This intermittent aeration mode is known to be more effective at maintaining the membrane permeability than continuous coarse-bubble aeration at the same overall air flow rate, and could become more widespread in the future.
The membrane air scour rate can be normalised against the membrane area to provide the specific air demand with reference to the membrane area (SADm). For most products no recommended values for the membrane air scour rate are provided with the specifications. For the Veolia ZW500
module, a design SADm value range of 0.098−0.196 Nm3/h air flow per m2 membrane area has been recommended based on practical experience at the landmark Henriksdal plant (Andersson et al, 2021). The lowest design SADm value range identified is 0.014−0.083 Nm3/(m2.h) for the Membion double-deck module.
Finally, a radical modification to reduce the SADm has been implemented by the Korean company Hifil (formerly Kolon). This technology laterally moves the membrane module to generate the shear by purely mechanical means, this being a lower-energy operation than blowing air.
4. Footprint
The module and cassette footprint can be defined in terms of:
- FA, membrane area per projected floor area, and
- FV, the membrane area per total module volume (i.e. the packing density).
The FA value for the modules varies between 98 and 1168 m2 membrane area per m2 floor area (Table 1), with a mean value of 666 and a standard deviation of 38% around the mean (Fig. 6). This compares to corresponding values of 197 to 572 m2/m3 for the module packing density FV, with a mean of 362±33% standard deviation. The variation does not appear to directly correlate with the fibre diameter, where packing density might be expected to be consistently higher for smaller fibre diameters, nor the module height (which would be expected to affect FA).
For the cassettes (Table 2), for which the parameter values are of more practical relevance, the data scatter is slightly reduced, with standard deviation values of 30% and 29% for FA and FV respectively. The mean values for these two parameters are 437 m2/m2 and 162 m2/m3 respectively, with the highest calculated packing density associated with the Memstar double-deck cassette (Fig. 7).
The decrease in the data scatter from module to cassette is unsurprising, given that the overall spacing of the fibres within the cassette must be sufficient to reduce the risk of clogging. The key operational parameters determining clogging propensity are the flux, air scour rate, and MLSS concentration. If these three parameters can be assumed to vary little between the different iHF products, then it follows that the packing density would also not be expected to vary significantly. In fact, if the low outlier is removed the cassette FV standard deviation decreases to 24%.
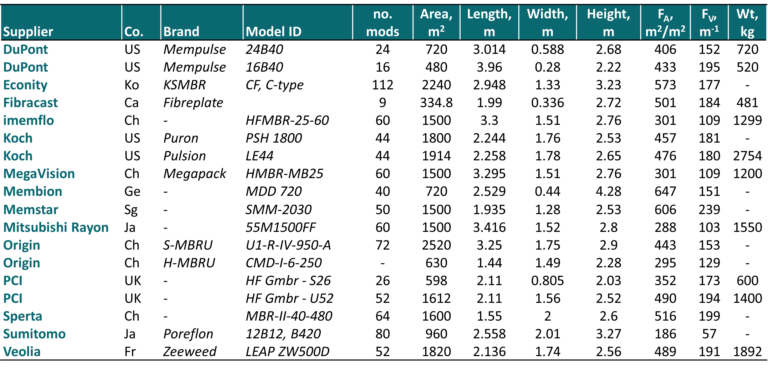
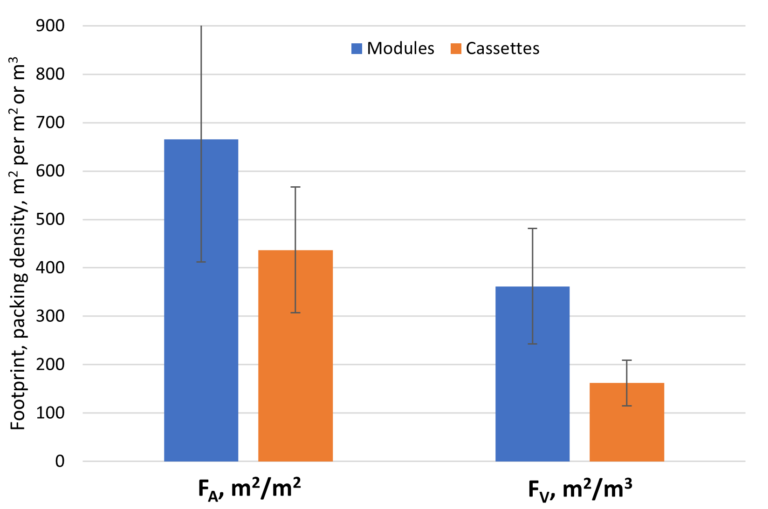
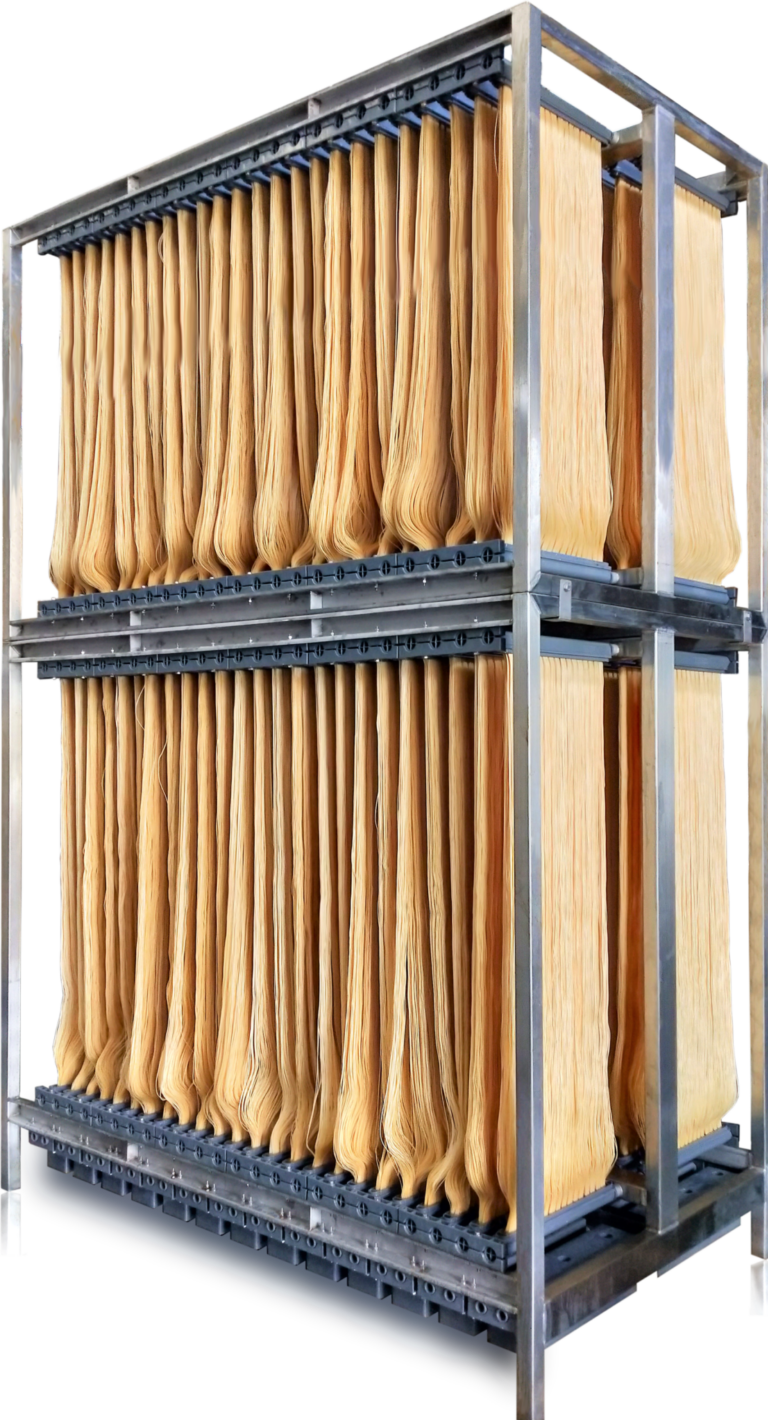
5. Conclusions
A review of the commercial hollow fibre modules used in immersed MBRs reveals them to be predominantly based on:
- polyvinylidene fluoride (PVDF) membranes of 1.9–2.8 mm outside diameter, 20–100 nm pore size, and with a braided core to provide mechanical strength
- rectangular modules of <0.1 m thickness and 1.5–2.4 m tall, and
- single-deck cassettes/racks of around 160 m2/m3 packing density.
Examples of variations from the above include:
- integrated membrane aerators providing intermittent high-intensity aeration, leading to lower overall membrane air scour rates
- modules configured as blocks
- alternative membrane materials (low and high-density polyethylene and PTFE)
- alternative geometries (square or cylindrical cross-section), and
- the use of housing for the individual modules.
The lower membrane air scouring rates of the iHF configuration mean that it will almost always be preferred for large-scale installations. The future of this technology therefore appears assured.