Membrane materials used in MBR technology: ceramic
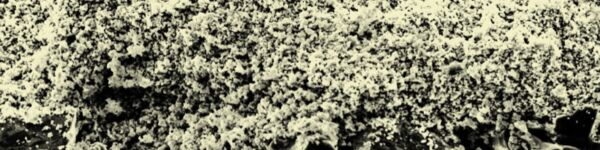
Ceramic membrane configurations: a brief history
Ceramic membranes first found use for solid−liquid separation duties within the food and beverage sector in the 1980s. Since the 1990s or earlier, they have also been used for other niche industrial effluent treatment applications (Lahiere and Goodboy, 1993; Chang et al, 1994, Judd, 2014).
They were first implemented as multitubes (i.e. as an MT configuration) for municipal potable water in 1996 at Miyazaki, Japan with a small (0.55 MLD) installation. By the end of the noughties there were 87 WTWs in Japan, delivering >400 MLD of drinking water (Hattori, 2010), based on the same vertically-oriented, cylindrical monolith MT membranes.
The mid−late noughties saw the implementation of the flat sheet (FS) ceramic membrane (Fig. 1) and module (Fig. 2), with its subsequent implementation for industrial process water and effluent and municipal potable water and wastewater applications (Binkle et al, 2005). The earliest ceramic membrane MBR installation was the 50 m3/d plant at St Wendel in Germany, which started up in 2005 and reused the treated water for toilet flushing. Most ceramic membrane MBRs that have been implemented since the mid 2010s have been the immersed flat sheet (iFS) configuration.
As well as the MT and FS configurations, ceramic membranes have also been commercialised as capillary tubes (CTs) − usually referred to as hollow fibre (HF), though the flow is always in-to-out (lumen-to-shell side). However, it is not apparent that these have been implemented.
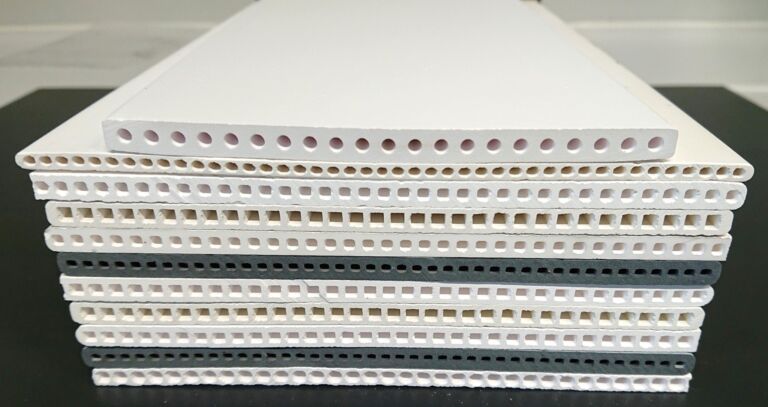
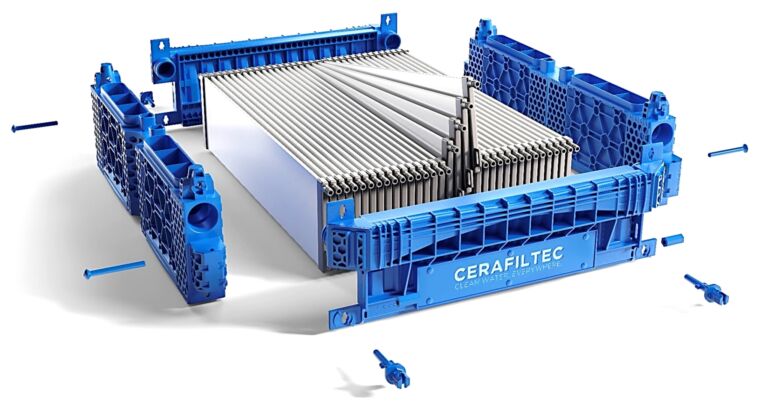
Membrane technology in water and wastewater
A membrane as applied to water and wastewater filtration is simply a material that allows water and dissolved matter to pass through it while rejecting solid particulate materials. It is ‘perm-selective’, with the degree of selectivity depending largely on the membrane pore size and pore size distribution.
Membranes for filtration are usually fabricated to:
- have a high surface porosity, or % total surface pore cross-sectional area
- have a narrow pore size distribution to provide as high a throughput and selectivity as possible
- be mechanically strong to give structural integrity, and
- be resistant to thermal and chemical attack, that is, extremes of temperature, pH and/or oxidant concentrations that normally arise when the membrane is chemically cleaned.
MBRs employ both polymeric and ceramic membranes, with polymeric membranes being the most established.
Ceramic membrane materials
Ceramic membranes are constructed of inorganic materials, predominantly metal oxides such as alumina/aluminium oxide (Al2O3), silica/silicon dioxide (SiO2), titania/titanium dioxide (TiO2), or zirconia/zirconium dioxide (ZrO2). They can also be formed from silicon carbide (SiC), mullite (3Al2O3·2SiO2), cordierite (Mg2Al4Si5O18), zeolites, and graphene (a form of elemental carbon). Of all these materials, only alumina, silica, titania, zirconia and silicon carbide have been commercialised for use in water and wastewater purification.
Ceramic membrane manufacture
As with polymeric membranes, ceramic membranes generally comprise a mechanically robust macroporous layer which provides a supporting structure for the ‘active’ membrane layer. The membranes are generally formed from powders of the bulk material through a two-step process:
- the production of the substrate, usually having a 1−10 micron pore size, by extrusion, sintering and drying, and
- coating of the dried substrate by spraying it with a slurry of fine particles (or else dipping the substrate into the slurry), followed by sintering and drying to form the final membrane product.
The slurry is a mixture of the powdered ceramic membrane material combined with plasticisers and solvents. Sintering (or firing) demands temperatures typically between 1000 °C and 2000 °C depending on the ceramic material. This step both removes binders and other organic volatile components and bonds the ceramic particles together to form a perm-selective, 3D material whose pore size depends both on the ceramic particle size and the precise processing protocol.
Ceramic membrane selectivity
The selectivity of commercially-available ceramic membranes for water and wastewater treatment is in the UF/MF region, but most often in the MF range of 0.1−0.5 µm. Nanofiltration products, such as from Ionopore and Cerahelix, are also available but are targeted at high-end separations rather than for water and wastewater treatment.
Commercial suppliers of ceramic membranes
Ceramic membrane technology is offered by several suppliers (Table 1). Its implementation for drinking water and, in particular, wastewater treatment is currently limited, though its use in potable water applications is becoming more widespread. Of the suppliers listed, those known to have MBR references − as of January 2025 − include CERAFILTEC, Meidensha and Ovivo.
Supplier | Country | Material | Configuration | Pore size, µm |
---|---|---|---|---|
*based on the ITN Nanovation product, acquired by SafBon in ~2018. | ||||
CERAFILTEC | Germany | Alumina | FS | 0.1–0.5 |
Ceraflo | Singapore | Alumina | FS | 0.5 |
LiqTech | Denmark | Silicon carbide | MT | 0.43–0.67 |
SafBon | China | Alumina | FS* | 0.1–0.5 |
Meidensha | Japan | Alumina | FS | 0.1 |
METAWATER | Japan | Alumina | MT | 0.1 |
Nanostone | US | Alumina | MT | 0.1 |
Pall Membralox | US | Alumina | MT | 0.2–1.4 |
Ovivo/Cembrane | US | Silicon carbide | FS | 0.1 |
Ceramic membrane costs
Ceramic membranes have been generally perceived as being too costly for wastewater MBR applications. However, total cost is dependent on both the flux and life of the membrane. Data on both these parameters from actual operating full-scale plant are limited. In particular, available data on membrane life are constrained by the limited age of the majority of the installations. Nonetheless, available data suggest, for municipal wastewater treatment:
- a design net flux of around 30−35 LMH (for the long panel design, such as Meidensha) and 40−45 LMH (for the block design, such as CERAFILTEC
- a membrane life of at least 20 years.
The use of a ceramic membrane material also introduces the possibility of reusing the membrane, should this be considered necessary or economically favourable, following re-firing of the spent membrane to remove the accumulated organic foulant material.
Benefits of ceramic membranes
In addition to the long life expectancy, the key advantages offered by ceramic membranes are associated with the inherent robustness of the ceramic material:
- the membrane life is typically 3-4 times that of polymeric membranes
- they cannot break, delaminate, or tear in the same way as a polymeric hollow fibre or flat sheet material
- they are resistant to oxidants (e.g. hypochlorite and ozone) and extremes of pH, permitting very aggressive chemical cleaning protocols
- they can operate in oily and coagulated conditions
- there is no mechanical limitation to backwashing
- there is no mechanical limitation to cleaning, such as through jet washing.