Low cost? Assumptions around costs in the MBR academic literature
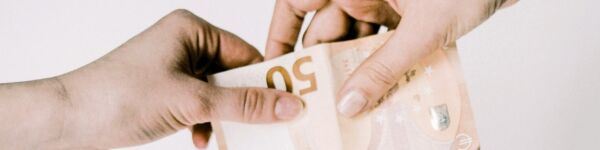
Simon Judd has over 35 years’ post-doctorate experience in all aspects of water and wastewater treatment technology, both in academic and industrial R&D. He has (co-)authored six book titles and over 200 peer-reviewed publications in water and wastewater treatment.
On ploughing through the published MBR research literature − not a task for the easily distracted − it is interesting how often the term ‘low-cost’ appears in the title, abstract or keywords of papers. Examples of MBR process modifications and enhancements that have been described in this way include:
- dynamically-formed membranes, where a membrane layer is formed in situ onto a low-cost substrate (such woven cloth)
- microbial fuel cells (MFCs), and
- alternative ceramic membrane raw materials, such as waste products.
The most common topic appears to be the first of these: the use of a ‘self-forming dynamic membrane’ (SFDM) in a ‘dynamic membrane bioreactor’ (DMBR). At least twenty studies have been published in the past fifteen years in which the SFDM has been described as ‘low cost’ in the paper's abstract.
Similarly, there have been around eight papers published over the same period that have described MFCs in the same way. The cost implications of MFCs have been discussed in a previous blog (Microbial fuel cells: something for nothing?). While there is undoubtedly a small energy benefit offered by MFCs, the practicalities of their implementation on a large scale, coupled with the high capital expenditure (CAPEX), challenges their implementation.
Finally, there are another ten papers on the subject of ceramic membranes partially-formed from carbon-based or other waste materials (including agricultural waste products such as rice husk, almond shells and olive stones).
Doubtless there are many more papers published within all the above areas that do not happen to use the term ‘low-cost’, ‘inexpensive’ or even ‘cheap’, to define these process adaptations. However, it’s pertinent to look a little closer at those that do – and the SFDM articles in particular.
The abstracts of these papers make interesting reading. None of the twenty SFDM/DMBR papers using the term ‘low-cost’ include any quantification of the cost benefit in the abstract (although this isn’t to say that such information is excluded from the full paper). The assumption of low cost appears to be essentially based on the cost of the membrane material, which is often a metal coagulant and/or a polymeric flocculant.
However, the capital cost of a membrane technology is not limited to the cost of the membrane material, i.e. the base polymer or ceramic. Other factors include:
- membrane fabrication: forming the membrane into a sheet, filament or tube, attaching it to a substrate and/or backing material, the firing temperature for ceramic membranes
- module construction, including the sealing of the membranes in the module
- skid construction: the mounting of an array of membrane modules within a frame and delivering flow evenly to each module
- quality control: ensuring that the maximum proportion of the membrane modules fabricated are fit for purpose, as demonstrated by integrity challenge and other tests, and
- membrane life and reliability that, along with energy and chemicals consumption, impact on the long-term operating costs.
Of course, it is easy to criticise. Experimentation is essential in delivering progress. It isn’t reasonable to expect a detailed cost analyses to be conducted with every single experimental investigation. In the same way, it isn’t possible to consider comprehensively the commercial implications of something that has only been tested within the confines of a laboratory.
But, as with many other popular areas of research (notably anaerobic MBRs), SFDMs are not without a commercial precedent. In the early/mid-1990s, there was a technology called Renovexx: a crossflow microfiltration process based on a ‘curtain’ of woven textile comprising a series of connected tubular channels (Gosling & Brown, 1993). An SFDM was formed on the inside of these tubes by dosing coagulant into the influent sewage and running the resultant suspension along the length of the tubes for a few minutes.
There was no significant issue with the overall effectiveness of the membrane: a fully-formed SFDM could clarify the sewage and provide reasonable pathogen rejection (and, presumably, phosphate removal as well). The membrane materials (the woven cloth substratum and the coagulant) were pretty cheap too. So, commercial success would surely follow, right?
Well, actually, no. By the turn of the Millennium, the Renovexx technology had pretty much run its course. The process was subject to significant downtime associated with the formation of the membrane and, over an extended period of operation, the substratum required vigorous mechanical cleaning to restore permeability − reducing its projected life to below two years. The membrane module had to be very long to reduce the number of connectors and achieve a reasonable conversion, and collection of the permeate along the entire length of the tubes was somewhat unwieldy.
Most crucially, despite the low cost of the woven cloth and the coagulant-based DFM, the cost of the entire crossflow microfiltration unit was higher than that of conventional clarification by coagulation followed by media filtration. Also, the SFDM could not reject pathogens as robustly as commercial polymeric MBR membranes. As a polishing process, the costs didn’t add up, and so was never likely to be cost competitive for use as an MBR.
And therein lies the rub. The most important attribute of a new process is the extent to which it substantially improves the status quo. The most comprehensive way of assessing this is through life cycle assessment (LCA). Failing this, a back-of-envelope cost analysis is normally sufficiently persuasive.
Last but not least, historical references are usually very informative. Sure, we should all learn from our mistakes. But, to paraphrase Warren Buffet, it’s cheaper to learn from someone else’s.