MBR CAPEX costs – large versus small
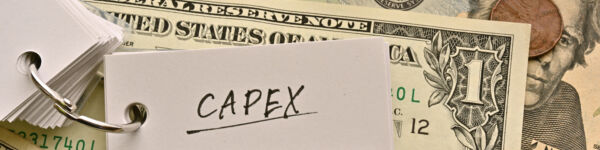
Simon Judd has over 35 years’ post-doctorate experience in all aspects of water and wastewater treatment technology, both in academic and industrial R&D. He has (co-)authored six book titles and over 200 peer-reviewed publications in water and wastewater treatment.
Over the past decade, there’s been a dawning realisation that MBRs aren’t necessarily the high-cost, high-performance option they were originally perceived as being up until around the mid-noughties. One of the most detailed cost analyses that’s ever been published (Young et al, 2013−14) concluded that an MBR worked out marginally cheaper, on a 20-year whole-life cost basis, than a classical ASP provided (a) nutrient removal was required and (b) peak loading factors were not too severe. This was for a 19 MLD (megalitres per day) plant.
According to that analysis, the margins are very small at 5−8%, with the outcome sensitive to many factors, including the membranes themselves. Membrane life and replacement costs represent one of the trickiest issues in MBR cost analyses. Most recent membrane life studies seem quite encouraging (Côté et al, 2012). An assumed life of 10 years may once have appeared over-ambitious, but for municipal applications this now seems to be the benchmark, if suppliers’ warrantees are anything to go by (and that’s another debate in itself).
Smaller-scale cost analyses
Published studies have almost all focused on large-scale municipal plants, often benchmarking costs against a classical activated sludge process (CAS). There have been very few cost analyses based on smaller scales, with the exception of a fairly rudimentary study of containerised plants (Fletcher et al, 2007). Given that MBRs are still regarded by some − wrongly, it would appear − as being most appropriate at small scale, it’s worth looking at this scenario more closely.
A very recent analysis (Lo et al, 2015), courtesy of the company Ecologix in Taiwan, deconstructed the MBR technology of a small-scale plant into its constituent parts. Unsurprisingly, when the individual components of MBR technology were considered, it is the membrane itself which makes up the lion’s share of the capital cost (CAPEX) – and increasingly so for larger plants.
If the capital cost curve based on the Lo et al (2015) analysis is extrapolated to the high capacities considered by Young et al, as well as others (DeCarolis et al, 2007; Brepols et al, 2010), the CAPEX is considerably lower than in the previously reported data. Against this, the extrapolated trend for operating costs (OPEX), based on a logarithmic relationship, runs almost straight through the data points reported for the larger municipal plants.
And, if you’re curious (or even if you’re not), the exact reported relationship determined is:
OPEX being in 2015 USD and Q being the flow capacity in m3/d.
So, what does this tell us? Well, firstly, trying to compute capital cost is something of a fool’s game. There are a huge number of variables and assumptions to which CAPEX is ultimately very sensitive. For a small containerised plant, the simple act of digging a hole to bury it can make up a significant part of the CAPEX, according to Fletcher et al. And the exhaustive analysis of Young et al elegantly demonstrates the impact of the price of concrete, equipment, land and labour for larger plants.
OPEX, on the other hand, is perhaps a little easier to grasp because it is largely made up by energy demand and critical component replacement (i.e. the membrane). The relationship is unlikely to be universally accurate, but the depicted trend is probably a reasonable reflection of the intuitive shallow decline in OPEX at increasingly large flows.
And, when all’s said and done, any cost estimate based on a reasonable set of assumptions is far better than no cost estimate at all, even if it is done on the back of an envelope.