Anaerobic membrane bioreactor (AnMBR) process control
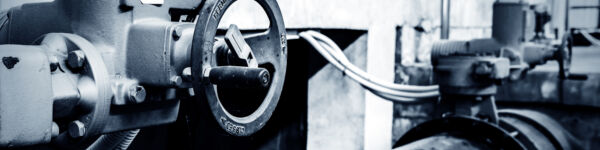
Ángel Roblesa, Maria Victoria Ruanoa, Amine Charfib, Geoffroy Lesagec, Marc Heranc, Jérôme Harmandd, Aurora Secoa, Jean-Philippe Steyerd, Damien J. Batstonee, Jeonghwan Kimf, José Ferrerg
aCALAGUA – Unidad Mixta UV-UPV, Departament d’Enginyeria Química, Universitat de València, Avinguda de la Universitat s/n, 46100, Burjassot, València, Spain
bLG-Hitachi Water solutions, B-1104 Daewoo Technopark, 261, Doyak-ro, Wonmi-gu, Bucheon-si, Gyeonggi-do, 14523, South Korea
c Institut Européen des Membranes, IEM – UMR 5635, ENSCM, CNRS, Univ Montpellier, Montpellier, France
d LBE, Univ Montpellier, INRA, 102 avenue des Etangs, 11100 Narbonne, France
e Advanced Water Management Centre (AWMC), The University of Queensland, QLD 4072, Australia
f Department of Environmental Engineering, Inha University, Incheon, South Korea
g CALAGUA – Unidad Mixta UV-UPV, Institut Universitari d'Investigació d’Enginyeria de l’Aigua i Medi Ambient – IIAMA, Universitat Politècnica de València, Camí de Vera s/n, 46022, València, Spain
1. Introduction
The increasing interest in anaerobic MBRs (AnMBRs) relates largely to resource recovery and the circular economy. Anaerobic treatment permits energy recovery through conversion of the organic carbon (OC) to a methane biogas, rather than the considerably more energy-intensive aerobic process which converts the OC to carbon dioxide. Aerobic systems also generate larger amounts of biosolids. Lastly, any aerobic process − whether or not combined with denitrification through the Modified Ludzack-Ettinger (MLE) process − results in the conversion of the ammonia to a less useful product. Ammonia itself can be a useful resource.
Integrating membrane separation with anaerobic treatment offers similar advantages to the conventional aerobic MBR, i.e. prolonged solids retention time (SRT) and a clarified effluent, but it also recovers resources. The increased SRT in part compensates the slower growth of anaerobic microbes compared with aerobic ones. However, AnMBRs are also more significantly constrained by membrane fouling than the aerobic equivalent, although advances in membrane technology have meant that competitive fluxes can be obtained.
The most established AnMBR configuration commercially is the sidestream (AnsMBR, Fig. 1a), where the high shear operation can promote higher fluxes. It is particularly suited to high-strength wastewaters (WWs) of high fouling propensity. However, the energy input for such operation is relatively high.
More recently, the immersed configuration (AniMBR, Fig. 1b) has been successfully implemented, in which the biogas is used to scour the membrane in the same way as air is used for an aerobic process (also discussed in the following video).
MBR Insights − Anaerobic vs aerobic mbrs
While the AnMBR technology offers the key advantage of resource recovery over the aerobic equivalent, and provides a higher treated water quality as well as greater flexibility and operational resilience over the classical non-membrane process, it is nonetheless constrained by:
- membrane fouling, and subsequent cleaning requirements, and
- dissolved methane and nutrients in the treated water, which may demand further treatment.
Extending the implementation of AnMBRs relies on addressing both of the above constraints, and specifically the operational efficiencies required for reducing the overall energy consumption whilst maintaining the product water quality. Many reviews of the area have focused primarily on membrane fouling. However, of arguably equal importance is the control of the process with reference to both the biology and the membrane separation components.
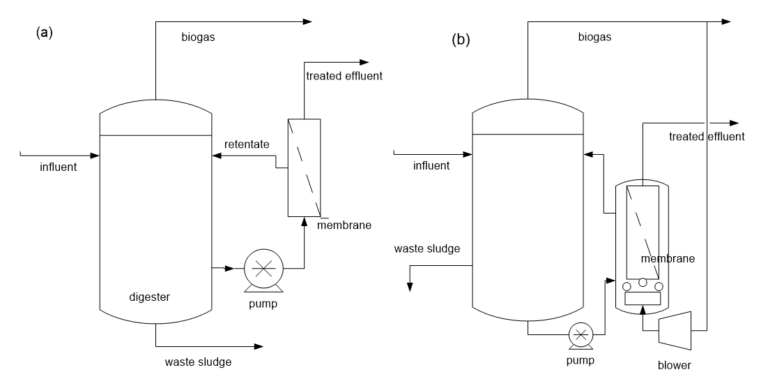
2. Control of AnMBRs
AnMBRs must be optimized to enhance energy production and resource recovery with minimum energy input. Optimization is made complex by the sensitivity of some microorganisms in the biomass to things like process overloads, variations in acidity and C/N ratios, and toxic shocks causing inhibition, foaming, rheological changes and other biological process upsets. These may then also impact on membrane surface fouling and membrane channel clogging. Effective control strategies are therefore important to optimize both biological and filtration operations.
Different control tools have been proposed from simple flux control to advanced control for both the anaerobic biological process and membrane filtration, particularly in the last two decades. However, unlike aerobic MBR technology, few control strategies have been developed and validated to optimize AnMBRs filtration performance.
2.1 Biological process control
Most of the available control strategies used for classical anaerobic treatment, specifically anaerobic digestion (AD), can be adapted for AnMBR optimization if the impact of the process biology on the membrane permeability can be taken into account. Process control strategies applied (Fig. 2a) have generally focused on substrate feed control, aimed at stabilizing the process and both maximizing methane production and complying with effluent criteria whenever required. Depending on the control objectives, the process variables selected can be methane flow rate, effluent COD and volatile fatty acid (VFA)/alkalinity ratio. This type of control uses feed flow or dilution as manipulated variables. When more than one substrate is involved in the anaerobic process, the other substrates are determined based on boundary conditions such as organic loading rate (OLR), hydraulic retention time (HRT), and C/N ratio. Other AD control strategies have employed chemical control (dosing with caustic soda, for example, to control alkalinity and pH), temperature control, and hydrodynamic control (to tackle foaming, for example) by modifying liquid/sludge recirculation rates.
Feed control with alkalinity/pH/mixing control is predominantly used in a cascade configuration to achieve a performance objective, such as maximizing methane production, and/or stability objective, based on pH, VFA concentration, etc. Examples explored in conventional AD include a standard PID-cascade (proportional−integral−derivative) for sustaining methane production while maintaining a low VFA set-point (García-Diéguez et al., 2011). Advanced controllers have included rule-based, fuzzy, artificial neural networks, model-based, and linear control systems. A neural network has been used to maximize methane production and COD degradation by manipulating the OLR on the basis of pH, VFA, and biogas production and composition (Holubar et al., 2003). For AnMBR processes specifically, OLR control through manipulating the filtration to relaxation ratio has been proposed based on the feed solids concentration (Robles et al., 2015).
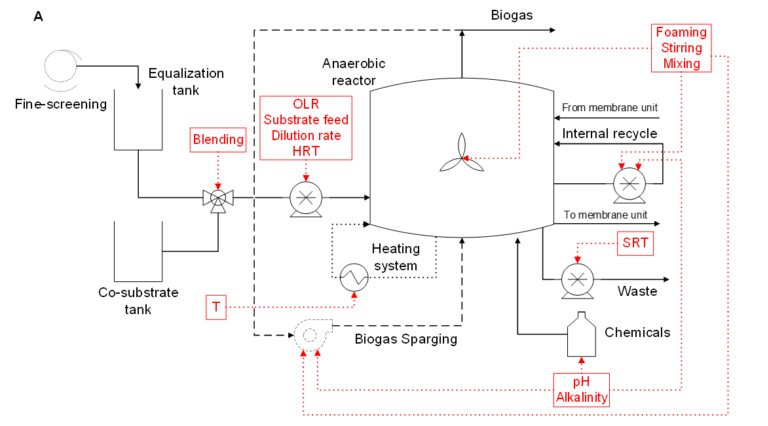
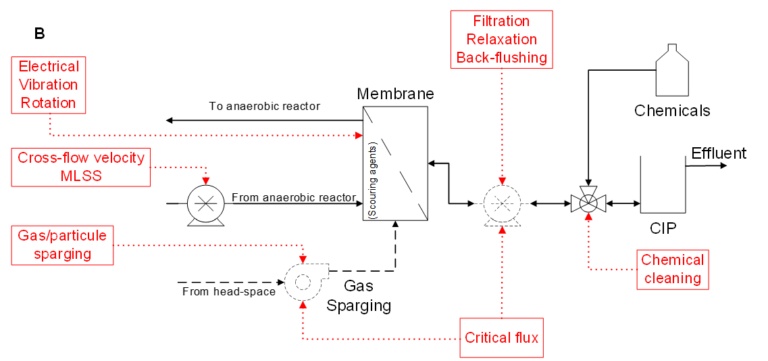
2.2 Filtration process control
Two types of terminology are commonly used for classifying the filtration control systems in MBRs:
- those relating to the nature of the controlled and manipulated variables, and
- those relating only to the nature of the controller.
In the first case, the filtration control systems usually involve the regulation of gas scouring (or crossflow velocity for an sMBR), flux, filtration and backflush/relaxation cycle duration and intervals, and chemical cleaning protocol and interval (Figure 2b).
In the second case, the control systems are classified as open-loop or closed-loop − i.e. without or with automatic regulation respectively. For open-loops, control does not depend on the actual state of the system. For instance, a specific filtration/backwash sequence may be advocated for a particular application. The open-loop mode has simple, inflexible operating strategies for fouling mitigation, as indicated by the transmembrane pressure (TMP) or permeability.
Against this, closed-loop control provides automatic regulation of a process variable to a desired state or set point. This then demands a degree of complexity beyond that of open-loop control. While a range of process operating strategies has been proposed and implemented for aerobic systems to minimize energy consumption through fouling control, similar information for fouling control in AnMBRs is more scarce.
2.2.1. Open-loop control
Developments in open-loop control of AnMBRs have generally mirrored that for aerobic systems. Operating strategies for open-loop membrane fouling control comprise physical cleaning, i.e. gas scouring (and ancillary scouring agents), and backflushing/relaxation, and chemical cleaning (Table 1). Since gas scouring accounts for a significant proportion of the total energy consumption, much effort has been focused in recent years on optimizing gas sparging intensity in AniMBR technology. This has included the use of scouring agents, such as activated carbon, to provide additional mechanical cleaning (Aslam et al., 2017).
Bioreactor configuration | Membrane information | Fouling control | References |
---|---|---|---|
Nomenclature: FS: flat-sheet; GAC: granular activated carbon; HF: hollow-fiber; PAC: powdered activated carbon; PE: Polyethylene; PVDF: polyvinylidene fluoride; PTFE: polytetrafluoroethylene; PES: polyethersulfone; and GAC: granular activated carbon. | |||
Completely mixed anaerobic reactor | 0.1 µm PVDF cross flow tubular | Cross-flow; weekly cleaning with 0.1% w/w NaOH and disinfectant | Baek and Pagilla, 2006 |
AnMBR | Cross-flow micro filtration | Critical flux | Jeison and van Lier, 2006 |
Immersed AnMBR | 0.4 µm FS | PAC/GAC+biogas sparging | Hu and Stuckey, 2007 |
Completely mixed anaerobic reactor | 0.2 µm cross flow HF | Periodic back-flushing; chemical cleaning with 0.1 M NaOH, 1% H2O2 and 1% HCl; and periodic back-flushing | Lew et al., 2009 |
Up-flow anaerobic reactor | 100 kDa cross flow coated PVDF and 30 kDa cross flow polyetherimine | Cross-flow velocity | Gao et al., 2010 |
Immersed AnMBR | 0.07 µm PVDF immersed HF | Biogas sparging | Park et al., 2010 |
Completely mixed anaerobic reactor | 0.1 µm PES immersed FS | Biogas sparging | Huang et al., 2011 |
Two-stage fluidised bed MBR | 0.1 µm PVDF immersed HF | GAC fluidisation; periodic back-flushing and/or NaOCl/NaOH cleaning | Kim et al., 2011 |
Immersed AnMBR | 0.03 µm HF | Critical flux | Robles et al., 2012 |
Immersed AnMBR | 0.03 µm HF | Backwash/biogas sparging/relaxation | Robles et al., 2013 |
AFMBR | 0.4 µm PVC FS | GAC | Aslam et al., 2014 |
Immersed AnMBR | 0.4 µm FS | Biogas sparging/Critical flux | Fox and Stuckey, 2015 |
AnMBR | 20-PVDF HF | Cross-flow velocity | Hu et al., 2017 |
Immersed AnMBR | 0.45 µm FS | Alternate biogas sparging | Zhang et al., 2017a |
Immersed AnMBR | 0.4 µm FS | Various adsorbents/foulants | Zhang et al., 2017b |
UASB-AnMBR | 0.3 µm PVDF immersed FS | Critical flux | Mahmoud and Liao, 2017 |
AFMBR | 0.5 µm Flat-tubular | Silica/Fluidized polyethylene terephthalate beads | Charfi et al., 2018 |
Microbial electrolysis cell + AnMBR | 0.01 µm PVDF immersed HF | Electric field by microbial electrolysis cell | Ding et al., 2018 |
Other less conventional methods for fouling include chemical modification of the mixed liquor using coagulants and flocculants (Zhang et al., 2017b), and electrically-assisted fouling mitigation (Ding et al., 2018).
2.2.2. Closed-loop control
Closed-loop control provides more operational robustness at the expense of a greater process complexity. Various studies have resulted in recommended strategies for control of the fouling (or cake) layer thickness or permeability, achieved through initiating backwashing at some set point determined through modelling and/or real-time data processing. Such approaches have extended to optimization of the gas scour, for example through fuzzy-logic control (Robles et al., 2014) to reduce the gas scour rate and so commensurately decrease (by up to 25%) energy consumption for iMBR membrane operation.
Control approaches involving optimal control theory have been also proposed to maximize filtration process productivity, thus achieving a certain optimality criterion (e.g. a cost function) based on a control law for a given filtration process. This has been applied to duties such as beer microfiltration to minimize the energy cost associated with backwashing (Cristea et al., 2013). A multi-objective control scenario has also been defined by Paulen et al. (2015) based on the Pontryagin Maximum principle − an advanced mathematical optimization process. This approach was used to predict the optimal times for switching between periods of filtration and backwashing for maximizing the net water production for a membrane filtration process based on a virgin membrane (Cogan et al., 2016), and subsequently under conditions encompassing membrane fouling (Kalboussi et al., 2018).
3. Outlook
While advanced closed-loop process control developments appear to offer promise, their application to AnMBRs is still at an early stage.
Biological modelling of anaerobic processes is reasonably mature, and mainly depends on the process application and type of substrate. Based on a general classification of substrates as low-strength WW, high-strength WW, and solid waste as a sole substrate or as a co-substrate, different control approaches are required to maximize methane production while maintaining process stability and effluent criteria.
For low-strength WW, usually characterized by high influent flows (i.e. sewage), control objectives are focused on meeting effluent criteria in terms of COD and maintaining a relatively high flux. In this case, the SRT and sludge recycling ratio (SRR) are the only practicably adjustable variables − with, possibly, feed blending to adjust the OLR if a high-strength stream is available.
In contrast, more controllable variables are available for high-strength, low-flow WW treatment or solid wastes in AD applications, including temperature, SRT, HRT, OLR and SRR. In this case, most of the conventional AD process control strategies can be applied to AnMBRs, provided HRT and SRT can be manipulated separately and so offer further optimization.
Against this, advanced filtration control in AnMBRs remains largely unexplored, despite the recent progress in optimal control theory and specifically the work based on the Pontryagin Maximum principle. Unsurprisingly, process control for the anaerobic process is less well developed than the more commercially significant aerobic iMBR. Significant advances in open-loop control have been achieved, however, due to improved understanding of fouling, though further progress is still needed to minimize downtime related to relaxation/backflushing.
Generally, closed-loop control is based on feedback or model-based approaches, although knowledge-based (e.g. fuzzy logic) controllers have also recently been explored. The main drawback of model-based control approaches is the complexity of the mechanisms involved, which make it impossible to describe fouling exactly and build a deterministic filtration model. Due to the highly non-linear relations arising in the physical separation processes and the large number of underlying filtration mechanisms, the results achieved by model-based controllers are only acceptable when the process dynamics are bounded by well-defined linear relationships. Also, most of the filtration models used for control design are limited to the description of fouling dynamics and ignore the process biology. This means that the impact of fouling control measures on the process biology are overlooked.
Further practical barriers to implementation include the absence of robust and reliable online instrumentation and limited demonstration of the advantages of these strategies.
In many ways, the implementation of advanced control strategies for AnMBRs faces similar challenges to other areas of MBR technology generally. There is a wealth of knowledge on foulant speciation and correlations between foulant generation and membrane filtration performance under controlled conditions. However, there remains a lack of understanding of such relationships under full-scale conditions where conditions are highly variable and the foulant materials and their dynamic behaviour highly heterogeneous. The challenge is made considerably greater in the case of AnMBRs by the much lower level of implementation of the technology itself at full scale. However, given the huge significance of the technology in the rapidly developing circular economy, it is becoming increasingly important that this challenge is met.