MBRs in municipal applications − lessons learned
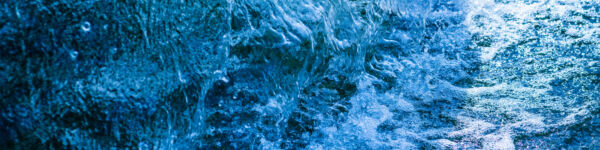
Christoph Brepols
Christoph Brepols is Project Manager, Wastewater Technology at Erftverband, Germany and author of ‘Operating Large Scale Membrane Bioreactors for Municipal Wastewater Treatment’. Email: [email protected]
1. Introduction
The German river association Erftverband has been into MBRs for municipal wastewater treatment for more than a decade, installing the first such system in Germany and commissioning what was the largest membrane bioreactor in the world. The company’s experience in MBR operation provides a valuable insight into the technology.
2. Plant Layout
The MBR is now established as the state-of-the-art technology for high-quality municipal wastewater treatment. Erftverband first conducted pilot trials based on the technology in 1996. This testing finally led to the commissioning of three full-scale MBRs now serving the association area. In 1999, the first municipal installation of its kind in Germany went into operation; five years later the Nordkanal MBR (Figure 1) became the world’s largest MBR at that time. The most recent project saw a membrane filtration facility replace the secondary clarifier of a conventional activated sludge plant, almost doubling the plant’s capacity.
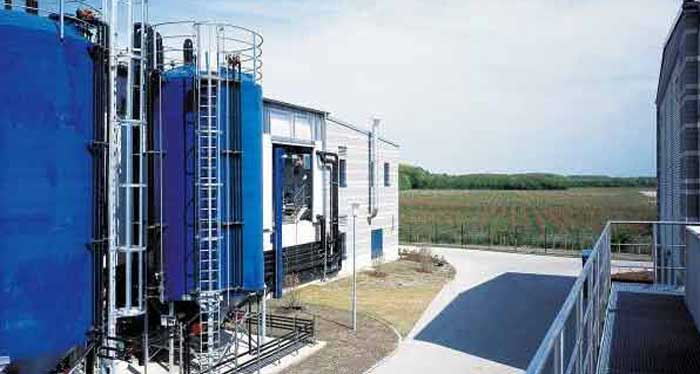
The Glessen MBR (Figure 2) has been operative since 2008 and is dedicated to improving water quality in a drinking water catchment area. All the plants employ hollow fibre microfiltration units that differ in size and layout (Table 1). Throughout the years efforts were made to optimise the design and operation of the plants to further increase the effluent quality and operational availability, while reducing energy consumption and operating cost. Although not without challenges, this has resulted in the long-term sustainable operation of all three plants.
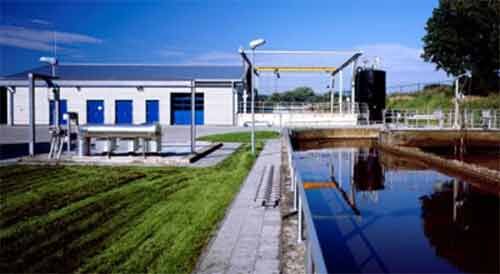
Besides the three MBRs, Erftverband owns and operates 44 municipal wastewater treatment plants (WWTPs), with a total capacity of 1.06 million population equivalents (PE). Many of these plants employ additional tertiary treatment with sand filtration or post-nitrification to meet stringent discharge criteria.
3. Effluent quality and nutrient removal
The biological treatment process was originally designed as simultaneous aerobic sludge stabilisation, with a sludge retention time of more than 25 days. This is also common for many conventional activated sludge plants, but MBRs differ widely in terms of biomass concentration and hydraulic retention time. The initial experience at the Rödingen MBR showed that for the given membrane system, sustained operation with biomass concentrations exceeding 15 kg/m³ of mixed liquor suspended solids led to increasing accumulation of stagnant biomass in the filter cassettes, and so a reduction in membrane performance.
Rödingen: 3000 | PE Glessen: 9000 PE | Nordkanal: 80,000 PE | |
---|---|---|---|
Commissioned | 1999 | 2008 | 2004 |
Dry / rain weather inflow | 300 / 3200 m³/d | 2000 / 6500 m³/d | 12,000 / 45,000 m³/d |
Bioreactor volume | 400 m³ | 1600 m³ | 9300 m³ |
Filtration tank volume | 80 m³ | 320 m³ | integrated |
Membrane surface | 5280 m² in 2 lines | 12,100 m² in 4 lines | 84,480 m² in eight lines |
The company’s other MBRs were therefore designed with lower MLSS concentrations that still allow enough room for inevitable concentration variations during actual operation, whilst still one third of the size of comparable conventional reactors. The hydraulic retention time is thus reduced by two thirds, and impacts on the dynamics of the biological process. Although the average removal rates of MBRs can be the same or even slightly higher than in comparable conventional activated sludge plants (see Figure 3), the variations in effluent concentrations are more pronounced. Oxygen carry-over induced by membrane air scouring, and the inevitable sludge recycle, may also impede denitrification if the process is not correctly designed and operated.

All three MBRs are operated with simultaneous phosphorus precipitation using ferric chloride. Some increase in biological phosphorus removal was also observed. It is assumed that anaerobic micro-zones inside the compact biomass flocs could be responsible. It has to be acknowledged that trimming down the phosphorus effluent concentrations by massive overdosing of precipitants may increase inorganic fouling on the membrane surface, and ferrous residuals inside the fibres and permeate pipes may interfere with the chemical membrane cleaning.
The membrane filtration is capable of achieving disinfection of the effluent. Grab samples are regularly analysed for microbial pollution. No significant deterioration in disinfection over time has been observed so far.
4. Energy consumption
Energy consumption has often been perceived as a main drawback in the application of MBR technology, and the main driver is the air scouring of the membrane filters. Compared to the first operational experiences, a substantial reduction has already been achieved by optimising the operational regime and the plant equipment. For example, the specific energy consumption of the company’s conventional activated sludge plant with tertiary treatment ranges between 0.5 and 1.8 kWh per cubic metre of wastewater treated. The Nordkanal MBR consumes 0.9 kWh/m3, with the air scouring alone being responsible for roughly one half of the energy consumption. Process aeration in the bioreactor, biomass circulation, bioreactor mixing and permeate suction together make up about one quarter. The remainder is consumed by pumping stations, pretreatment, sludge dewatering and miscellaneous process units.
The Nordkanal MBR treats mixed sewer influent and thus there is abundant membrane surface during dry weather. The process control of the membrane filtration was originally designed with extreme caution towards the hydraulic performance during storm weather. The past operational experience gave the confidence that maximum inflow can be treated efficiently. On the other hand, it became obvious that the energy efficiency of the process decreases dramatically at times of low inflow (Figure 4). Dry weather conditions with less than a third of the maximum design flow prevail for more than two thirds of the year, significantly affecting mean energy demand. Currently, a new process control scheme is being installed to reduce aeration demand by improving the flow distribution to the eight filtration lines. It is estimated that the energy consumption can thus be reduced by at least 20%.
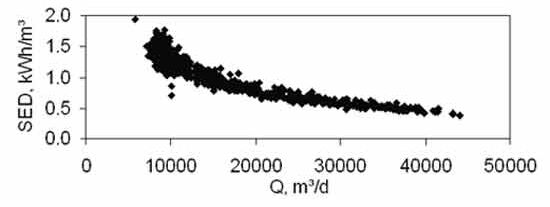
5. Membrane Maintenance
When the first MBR at Rödingen began operation it was still unclear as to the achievable membrane service life for municipal wastewater treatment. Unfortunately, after starting up the first plant, it was learned the hard way that an insufficient mechanical pretreatment of the wastewater together with an inappropriate cleaning strategy could hamper membrane filter performance within a few months. However, since overcoming these initial problems, the membrane filters have served for more than nine years, and it is planned to continue with them.
Today it is evident that membrane service life can be prolonged by adequate wastewater pre-treatment and proper plant design and operation. The employment of additional fine sieves in the influent prevents the clogging of membrane modules. Backwashing, relaxation and chemical cleaning of the membrane filters are the backbone of stable filtration performance. Depending on the size and the equipment of each installation, different cleaning strategies are applied to the MBRs. The ageing plant equipment and alterations of the membrane properties over time make regular revision of existing cleaning strategies inevitable.
The end of the membrane lifetime may result from mechanical failure of the membrane or the module construction or irrecoverable loss of filtration performance. However, the actual trigger for membrane replacement needs to be assessed individually. The practicability of replacing the existing modules by membranes of an alternative supplier was assessed in a pilot study. It could be seen that the successful migration to different membrane modules requires detailed engineering and well-considered changes to several process parameters.
6. Operational availability
The operational availability of a membrane bioreactor depends on several factors. Some of them are also common for conventional activated sludge plants, while others are linked to the properties of the process and the membrane filters. Possible failures can be categorised as external disruptions that come from the sewer system and internal disturbances and failures of design, equipment and operation of the plant. For example, harmful substances from the sewer, like coating agents, thinners or solvents from industrial processes, may lead to increased fouling or a disintegration of the membranes. Therefore, it is important to be aware of possible contributors that may exist in the sewer catchment area.
Malfunctions of the peripheral equipment like screenings, sieves, blowers and valves may cause severe disruptions of the filtration performance by braid formation (or ragging) on the filtration modules, or filter blocking. Thus, the critical parts of the equipment have to be maintained carefully and with prudence. The operators need to be aware of possible secondary effects that can be produced by the initial failures, and the diagnostic and counter-measures that then need to be taken.
7. Staff training
Fail-safe operation of an MBR requires a skilful and motivated workforce, or else the new technological system can severely challenge operators that are not accustomed to the process. In order to let others benefit from the lessons learned and to prevent them from repeating similar mistakes, Erftverband started to organise workshops on a national and international level to disseminate and discuss operational experiences among operators, consultants and policy-makers. Since 2005, Erftverband has been a partner in the SIMAS non-profit training centre for membrane operators. It provides comprehensive theoretical and practical training in the operation of membrane bioreactor systems and familiarises trainees with the use of different membrane systems.
8. Conclusion
Optimising the practical operations of an MBR process is a permanent task with regards to cost efficiency, technical reliability and compliance with environmental standards. In many cases the attainable effects of process optimisation are already limited by the original plant design. However, several measures have been developed that assure or even increase the long-term economic efficiency of MBRs under the given circumstances. Past achievements in research and development, but also in MBR operation, make MBRs today a viable and often advantageous alternative to more conventional wastewater treatment technologies.