Sustaining membrane permeability: a low-energy alternative to membrane air scour?
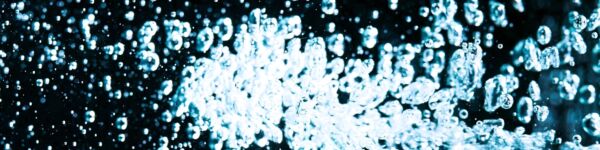
Simon Judd has over 35 years’ post-doctorate experience in all aspects of water and wastewater treatment technology, both in academic and industrial R&D. He has (co-)authored six book titles and over 200 peer-reviewed publications in water and wastewater treatment.
The broad implications of the latest iteration of the EU urban wastewater treatment directive (UWWTD) have been discussed previously. Clearly, there is a lot to unpack in the new legislation – particularly regarding greenhouse gases (GHGs). However, it is generally acknowledged that achieving energy neutrality must necessarily require a reduction in energy consumption.
The generally higher aeration demand of the immersed membrane bioreactor (iMBR) technologies compared with the conventional activated sludge (CAS) process would seem to work against their adoption. On the other hand, MBRs provide a degree of pollutant removal which is not generally attainable with CAS, and such enhanced pollutant removal forms another cornerstone of the legislation.
Much progress has been made in reducing the amount of air scouring required to maintain the membrane permeability in iMBRs, primarily through the design of the membrane aeration device and mode of air application. The specific aeration demand with respect to permeate production SADp, the ratio of the volume of air demanded to the volume of permeate produced, is currently around one tenth of that of the original immersed hollow fibre (iHF) technologies first implemented in the mid-1990s. However, even with this very significant increase in energy efficiency, iMBRs are still more energy intensive than the CAS process – simply because CAS does not require the supplementary air scouring demanded by the immersed membrane.
So, what more can be done? Let’s go back to basics.
Membrane air scouring, as is ubiquitously employed in iMBRs, is needed to:
- effect shear at the membrane surface to promote membrane permeation by suppressing membrane surface fouling (and so enhance the flux), and
- clear the membrane channels of the accumulating sludge solids (and so suppress clogging).
Fouling is roughly exponentially related to the flux. So, one way of sustaining membrane permeability with little or no air scour is by substantially reducing the flux. However, this then demands a commensurately large membrane area, which is unlikely to be cost effective and would drastically increase the embedded carbon of the process. Moreover, even with zero fouling the sludge solids would still need to be cleared from the channels to prevent clogging. So, the membrane separation process will always need shear.
Shear is created when a fluid moves parallel to a surface. It can be generated both by a rising air bubble (as in iMBRs) or by pumping the mixed liquor along the membrane channels, as is the case with the sidestream MBR (or sMBR) configuration (Fig. 1). Both these modes of shear generation are effective, but shear generated by air bubbles is less energy intensive than by liquid pumping.
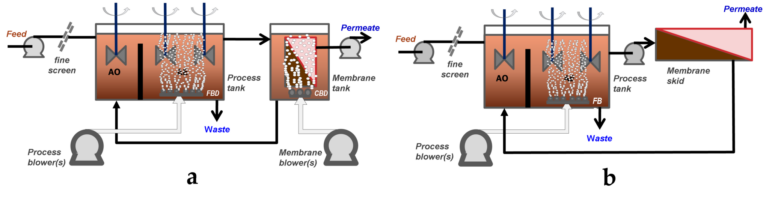
A look at some of the membrane specific energy consumption (SECm) figures reported for iHF MBRs over the years (Table 1) indicates the extent of progress made in energy efficiency gains in membrane scouring using air due to the reduction in SADp. With the exception of one outlier (Tang and Liu, 2019), the minimum SECm reported for an iHF MBR employing air scouring is around 0.18 kWh per m3 of permeate product. This would seem to be as low as it’s possible to go with air scouring.
Source | Date | SECm, kWh/m3 | Reference |
---|---|---|---|
*optimised; **accompanying SADp range of 9.1–22 Nm3/m3 | |||
Baseline figure | 2006 | 0.31 | Judd, 2006 |
Nine full-scale plant (ave. ± std. dev.) | 2010 | 0.22–0.36** | Judd, 2010 |
Pilot plant | 2014 | 0.29 | Ho et al, 2014 |
Pilot plant, 45m2 membrane area | 2015 | 0.19 | Ho et al, 2015 |
Full-scale plant, 3.2 MLD* | 2015 | 0.18 | Monclus et al, 2015 |
Full-scale plant* | 2019 | >0.049 | Tang and Liu, 2019 |
Model* | 2023 | 0.18 | Makisha, 2023 |
There is, however, an alternative. It has been recognised for some time that, rather than through moving the liquid across the surface of the membrane, shear can be generated more effectively by moving the membrane itself. This is the basis of the long-established VSEP technology from New Logic, which employs a vibrating membrane to achieve very high fluxes. VSEP
is not appropriate for an iMBR since the high shears would significantly degrade the biological process flocs, but the principle is applicable to any membrane process.
Moving immersed membranes have been explored at bench-scale since the mid-noughties (Beier et al, 2006). This area of study has since been extended to the pilot-plant scale. Work originally conducted under the auspices of Doosan Hydro Technology (Ho et al, 2014, 2015; Bae et al, 2020) has demonstrated a 66–85% reduction in SECm using laterally-oscillating (or ‘reciprocating’) membranes (Table 2). The technology has apparently since been commercialised (HiFil, 2024).
Source | Date | SECm, kWh/m3 | Reduction vs air scouring | Reference |
---|---|---|---|---|
Pilot plant | 2014 | 0.072 | 75% | Ho et al, 2014 |
Pilot plant, 45m2 membrane area | 2015 | 0.064 | 66% | Ho et al, 2015 |
Pilot plant | 2020 | 0.003–0.015 | 85% | Bae et al, 2020 |
So, shear really can be generated with greater energetic efficiency using a moving membrane than by using pumped air. So, why hasn’t this technology taken off? Where are the legions of implemented reciprocating iMBRs?
As is often the case, it isn’t just about the instantaneous energy efficiency. Were that the case, all aerobic MBRs would be fitted with microbial fuel cells, quantum quenching, oscillating membranes, and probably a host of other modifications or devices offering some sort of potential operational energy saving.
Firstly, there’s the capital cost implications. The CAPEX of a full-scale mechanical membrane oscillator is unclear, but given the complications associated with the physical movement of a number of large, bulky objects in a big tank it seems possible that its installation would be more costly than that associated with a blower. The membrane tank itself would almost certainly need to be larger given that the lateral movement of the membrane would incur a greater footprint.
Secondly, moving parts are more prone to failure due to mechanical stress. The constant flexing of the hoses due to the movement of the membrane modules is likely to reduce their life and require them to be replaced at regular junctures to reduce the risk of failure. While the equipment costs associated with this may be negligible, the labour costs could be more significant.
Lastly, in terms of improving operating energy efficiency in existing installed MBRs, there are other options which could be explored that would be expected to be more reliable. These include:
- improving membrane utilisation through flow equalisation (i.e. installing a buffer tank),
- automatic adjustment of the membrane aeration and/or operating membrane area with the feed flow through process control, and
- biological process aeration optimisation using advanced process control methods such as fuzzy logic.
Oscillating the membrane as an alternative to air scour offers a very elegant means of reducing energy consumption. However, like many apparently ingenious solutions, what may seem like a good idea in isolation is not always ideal in practice. But time will tell.