Thinking of setting up a membrane bioreactor? − Top 10 factors to consider
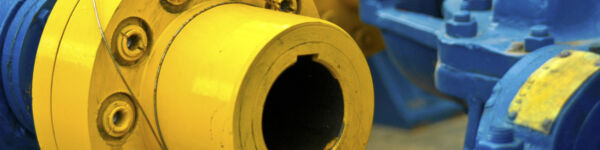
Simon Judd has over 35 years’ post-doctorate experience in all aspects of water and wastewater treatment technology, both in academic and industrial R&D. He has (co-)authored six book titles and over 200 peer-reviewed publications in water and wastewater treatment.
The factors governing implementation of an MBR (or any other technology, for that matter) can largely be reduced to a single parameter: money. There may be other motivating factors, but ultimately the emphasis on limiting costs (or reducing carbon footprint, to adopt the appropriate eco-speak) pretty much trumps everything else.
Granted, the technology has to be fit for purpose and this may demand some aspect of sustainability, but even this can ultimately be quantified in terms of the folding stuff. And it's pretty rare that the decision-makers will be banging the table and exclaiming, in angst-ridden tones, 'Godammit there's gotta be a way of making it more EXPENSIVE!'.
So, in the interests of keeping all those accountant-types happy, here's a list of the top 10 key factors to take into consideration when implementing an MBR. Note that they are in no particular order and are largely interrelated.
1. Feedwater quality
The organic carbon concentration will determine the process aeration (or, if high enough, whether anaerobic treatment may not be more appropriate). The N and P content will determine whether nutrient balancing is required. This is no different to any other biological treatment process.
2. Feedwater quantity
There is perhaps less economy of scale for an MBR than for a conventional process. However, MBR costs are most affected by the peak loading factor, since they must necessarily be designed for the maximum flow.
3. Design net flux
This directly determines the membrane requirement and the specific aeration demand with respect to permeate volume (SADp) for membrane air scouring.
4. Residuals
Sludge generation relates to the organic loading rate (OLR) and hydraulic and solids retention times (HRT and SRT), which then determine the mixed liquor suspended solids (MLSS) and food to microorganism (F:M) ratio − again, as with any biological process. Because MBRs operate at a higher MLSS, the sludge production is lower than for the conventional process.
5. Footprint
The reduced footprint of an MBR over a conventional process arises primarily from the higher MLSS.
6. Pretreatment requirements
Tighter screening reduces the risk of clogging of the membrane, but obviously generates more screenings demanding their own management.
7. Post-treatment requirements
UV disinfection or reverse osmosis (RO) can be carried out without an intermediate treatment step because of the high clarity and low silt density index (SDI) of the MBR permeate. The MBR permeate quality itself depends primarily on the process operating conditions (HRT and SRT), as well as on the robustness of the membrane.
8. Cost, capex
Primarily comprising equipment and installation (mechanical and electrical, civils, etc).
9. Cost, opex
Primarily comprising energy, membrane replacement and labour.
10. Cost, totex/whole life
Capex plus opex amortised over the envisaged life of the plant.
Capex (8) is directly affected by the flux (3), footprint (5), pretreatment (6) and post-treatment (7). Opex (9) is directly affected by the organic and hydraulic loading (1 and 2), flux (3), residuals (4) and pre/post treatment (6−7). Maintenance of the flux depends on the cleaning cycle and protocols, which add slightly to the opex (but not a great deal).
So, it's possibly a little complicated but, as with so many things in life, it all comes down to money. And what could be simpler than that?