How risky? PVDF membranes, PFAS emissions and environmental impact
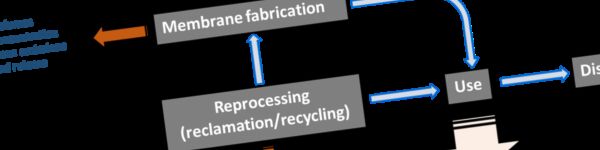
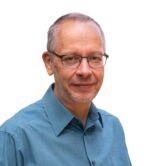
Simon Judd
Simon is a Director at Judd Water & Wastewater Consultants. This technical feature follows on from a recent guest blog from Graeme Pearce on the implications of the proposed EU REACH legislation on PFAS-containing products
1. The concept of risk
Life is a balance of risks. We all realise this and assess risk on a daily basis, if only subconsciously. It would be perfectly normal, for example, to nonchalantly cross the Boulevard Albert 1er at 7 o’clock on a February morning, but it would be foolhardy to do the same thing in May at the start of the Monaco Grand Prix.
Risk changes according to the circumstances. And so it is with the risk of PFAS emissions associated with PVDF membranes. There is undoubtedly such a risk over the entire life cycle of the membrane, but its nature and magnitude changes between the three stages of manufacture, use and disposal.
Quantifying risk is normally through a consideration of two components: frequency (or likelihood) and impact. In the case of pollution, the impact normally relates to, but is not limited by, the pollutant mass flow rate (concentration x volumetric flow).
2. The PVDF membrane life cycle
There are two steps to the PVDF membrane manufacture stage. Firstly, there is the production of the PVDF polymer from the perfluoroalkyl monomers (Fig. 1). Fabrication of the membrane then proceeds by dissolving the polymer in solution and precipitating the membrane material under controlled conditions, often onto some kind of substrate.
The resulting membrane can be configured as a flat sheet, hollow fibre or tube. All three of these configurations find use in commercial MBR technologies for wastewater treatment. For potable water treatment, it is mainly the hollow fibre configuration which is used. For both of these applications, the membrane life is usually between six and ten years.
The end of the use stage is generally determined either by a reduction in the permeability to a point at which continued operation is no longer viable, and/or by a loss of membrane integrity. Integrity loss is more of an issue in the potable water and water reuse applications than in wastewater treatment.
At the end of the use stage, the membrane material must either be reused or disposed of. There are no accepted commercial processes for reclamation and reuse of spent PVDF membrane modules, leaving disposal as the only current option.
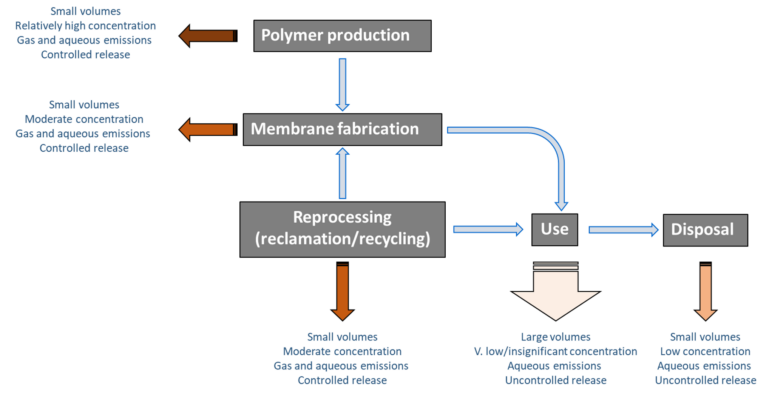
3. Environmental risk during the PVDF membrane life cycle
The EU is proposing to ban all PFAS materials completely as part of their REACH regulations. Any exemption ('derogation') may be granted on a temporary basis if a sufficiently strong case is made, but it must be assumed in the first instance that this will not necessarily be the case for the application of PVDF membranes to water and wastewater treatment.
But is there a case for retaining PVDF membranes, solely on the basis of the balance of environmental risk? This hinges around a number of specific issues, most notably:
- the relative environmental and health risks associated with the different stages
- the possible mitigation of these risks, and
- whether the alternatives to PVDF present a substantially lower overall environmental risk.
To address the above, a benchmark is needed for the level of PFAS in discharges which is likely to be acceptable. The two most extensively produced and studied PFAS compounds are PFOS (perfluorooctanesulfonic acid) and PFOA (perfluorooctanoic acid). The US EPA legal limits for these two PFAS species in drinking water, set earlier this year, is 4 ng/L for each. This reflects the perceived human health risk from ingestion; the level is, for comparison, 25 times lower than that set for pesticide residues (100 ng/L for an individual pesticide).
3.1 Environmental risk and mitigation
3.1.1 Fabrication
Production of PVDF polymer proceeds through the free radical polymerisation of 1,1-difluoroethylene (CH2=CF2, DFE), generating a polymer chain with repeated units of vinylidene difluoride (-CH2-F2-)n (Fig. 2).
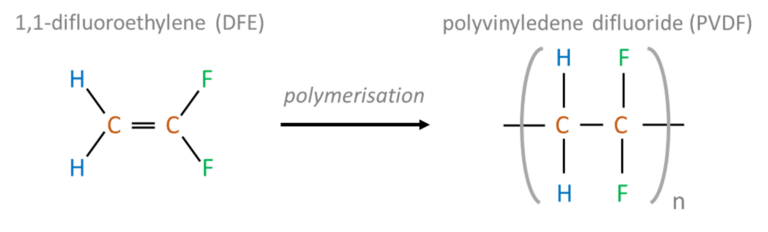
Given that there must be residual DFE reactant along with partly polymerised species – up to ~100 carbons in polymer chain length (i.e. n ~ 50 maximum) – at the end of the polymerisation process, there is an associated emissions risk for these species. There is at least anecdotal evidence that, in practice, discharges of PFAS from PVDF manufacturing facilities have taken place (Newton et al, 2017; Strynar et al, 2019). There does not appear to be any similar evidence of PFAS emissions from membrane module fabrication facilities, though it would be naive to completely discount this possibility.
A critical point regarding the manufacturing stage is the extent to which the wastewater streams can be recycled, thereby limiting the risk of emissions of trace levels of PFAS that they can be expected to contain. Emissions from venting of gaseous wastes can potentially be addressed using thermal destruction, though this is (a) highly energy intensive – demanding an operating temperature above 750 °C (Altarawneh et al, 2022), and (b) problematic in that the mineral product (hydrogen fluoride) is highly corrosive and other stable PFAS compounds can be generated as combustion side products.
Both PVDF polymer and membrane module production, while incurring a potentially significant environmental impact from emissions, are nonetheless operations which can be conducted with a high degree of control. The risk of emissions can be reduced through an appropriately robust process treatment scheme. This would encompass recycling of the majority of the water such that any discharged streams are low in volume and subject to rigorous processing – ultimately by combustion.
The reduction in volume, and the commensurate enrichment of the PFAS in these streams, for treatment is important. Methods proposed for PFAS removal from water include adsorption using anion exchange (Boyer et al, 2021) or activated carbon (Gagliano et al, 2020) and advanced oxidation (Veciana et al, 2022). Such processes are (a) relatively costly, and (b) likely to prove ineffective when other more reactive organic species are present at significantly higher concentrations than the PFAS. And, in the case of any separation process such as adsorption, there is no actual destruction of the PFAS; a secondary destruction process would be needed. Thus, for high-volume/low-pollutant concentration water and wastewater streams, treatment dedicated to PFAS removal is unlikely to be economically viable.
3.1.2 Use
The possible emission of PFAS from a PVDF membrane used for potable water treatment is assessed as part of the regulatory approval process. This process comprises a standardised leach test whereby water is recirculated through a membrane module under controlled conditions and the leach water then analysed for micropollutants.
Given that no membrane product can be approved for use unless it passes these leach tests, it must be assumed that any PFAS detected – if detected at all – has not been considered significant. As with PVDF membrane fabrication, there does not appear to be any data to support the suggestion that PFAS leaches from PVDF membranes during their use for potable water treatment and reuse.
Leaching of 'hydrophilic agent' from PVDF membranes has been reported from a painstaking examination of full-scale potable water membrane plants (Robinson and Bérubé, 2020), but this material appears to be the pore-forming additive polyvinyl pyrrolidone, or PVP, as noted by previous studies (Mavukkandy et al, 2016; Causserand et al, 2015). PVP does not qualify as PFAS.
3.1.3 Disposal
Emissions arising from the disposal of spent PVDF membranes do not appear to have been quantified. Given that spent membrane modules are generally landfilled, and therefore co-disposed with other materials, it must be assumed that any PFAS emissions would be manifested in the landfill leachate. PFAS has certainly been widely detected in landfill leachate (Capozzi et al, 2023), but has not been attributed to PVDF membranes disposal specifically. The most commonly-identified sources of PFAS in this effluent stream are coatings for textiles (including carpets) and food containers.
The alternative to landfill disposal is incineration. This is subject to the same challenges and constraints as thermal destruction of PFAS: it is unclear that incineration can reliably destroy all polyfluoroalkyl PFAS species (Aleksandrov et al, 2019).
3.1.4 Recycling
No apparent commercial processes exist for PVDF membrane reclamation and reuse. Based on the few research papers published in this area (Wang et al, 2017; Veiga et al, 2020), it appears that the recovered PVDF membrane material has a similar or improved permeability coupled with inferior mechanical properties compared with the virgin polymer (Wang et al, 2017). This may not preclude reuse of the recovered PVDF material for other applications (Veiga et al, 2020).
In all recycling applications, there is in any case a reluctance to employ reused PVDF material because of the likelihood of reduced integrity and possible cross contamination. There also appears to have been no attempt to reclaim the PVDF multiple times. Recycling thus represents a huge commercial risk, as well as a possible environmental one.
However, reclamation and reuse of waste material to fabricate a usable membrane has been successfully demonstrated for one type of membrane material. The REMEB ceramic membrane was created from waste olive stones, chamotte (a residue from the ceramic tile industry) and marble dust, and was installed at a WwTW in the Aledo region of Spain.
3.2 Alternative membrane materials
Alternative non-PFAS materials already exist for municipal applications, and include polyethersulfone (PES), polypropylene (PP), and ceramic membranes such as alumina, titania and silicon carbide. Since membranes based on these materials are much less prevalent than PVDF, it is reasonable to assume that they are considered less attractive options than PVDF in terms of economics, durability and/or other metrics. It is also uncertain as to whether polyfluoroalkyls are used in the construction of the modules based on these membrane materials, though it would presumably be possible to identify alternatives for these were this to be the case.
PES and PP are not polyfluoroalkyl materials, and therefore would not themselves be subject to the new legislative restrictions. As with PVDF membranes they generate effluents during their manufacture which require purification prior to discharge or reuse, but these effluents are much less likely to contain significant levels of PFAS.
PES membranes appear to be slightly less resistant to chemical cleaning than PVDF (Li et al, 2021), which would be expected to impact on the membrane life and/or the membrane permeability. This would then impact on the environmental footprint, but perhaps not to the extent of offsetting the impact of specialised disposal required for the PVDF membranes.
Ceramic membranes are recognised as being very durable and having a commensurately extended life compared with polymeric membranes in potable water applications (Judd and Carra, 2021), where implementation extends back more than two decades. Their application to wastewater treatment in MBR technologies is more recent, but anecdotal evidence suggests that an extended life over that for polymeric membranes can also be expected for this duty as well. The principal disadvantage of ceramic membranes is their higher cost, though the trend appears to be downward.
4. Conclusions
Emissions across the entire PVDF life cycle vary both in terms of prospective concentration and effluent volumes, with reference to both aqueous and gas streams. There are four stages to consider (excluding the possibility of reclamation and reuse/recycling), of which the actual use stage seems unlikely to generate significant emissions given the noted stability of the PVDF material.
There is currently little data on the actual levels of emissions of PFAS from PVDF membranes across their entire life cycle, though there is some evidence that emissions are associated with the initial PVDF polymer production stage. There appears to be no data to support the notion of PFAS emissions during the use of PVDF membranes, though this needs to be verified through site-based determination of permeate PFAS concentrations. Whilst it might be expected for emissions to take place at the disposal stage, data from landfill leachate suggest that PFAS emissions from these sites mainly derive from textiles and food packaging.
Recycling of PVDF may present a means of reducing the environmental footprint of PVDF membranes, but there are significant challenges to overcome if this option is to be pursued. The reprocessing/reclamation activity itself comes with an emission risk, and the reclaimed product may not be as reliably robust as the virgin material. Moreover, the cost of reprocessing may preclude it as a realistic prospect.
What is almost certain is that the costs associated with membrane technology implementation in the municipal water sector are likely to increase. As things stand, it appears that retaining PVDF as a membrane material option will require quantifying PFAS emissions over the membrane life cycle − particularly the production and disposal stages − to establish the environmental risk. Whilst obviously incurring a cost, this provides a huge opportunity for industry and academia alike to perhaps demonstrate the credentials of PVDF as a low environmental risk membrane option. Displacement of existing installed PVDF membranes with alternatives is not without risk, and will incur costs associated with the differing specifications of the alternative membrane. Alongside these challenges are the practicalities of enforcement of the legislation.
It is unquestionably the case that demand management represents the most effective − and perhaps the only − means of reversing the accumulation of PFAS in the environment. Whether this should include an essentially stable polymer that does not appear to emit PFAS during use, and which has proven efficacy in maintaining high treated water quality for key applications like water reuse, is perhaps more open to debate.
So, maybe a little less academic research on membrane fouling and a lot more on PFAS emissions. Just saying.