MABRs: Membrane aerated biofilm reactors and oxygenation
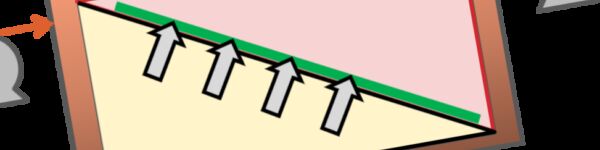
Membrane aerated biofilm reactors - an introduction
‘MABR’ stands for ‘membrane-aerated biofilm reactor’. An MABR is an alternative aerobic biological treatment process to MBRs (membrane bioreactors). It is an example of a ‘fixed film’ process - like a trickling filter - as opposed to a purely suspended growth process, i.e. one based on activated sludge (as is the case for the MBR).
In an MABR, the membrane (often a hollow fibre) is used as an alternative aerator, rather than for biomass separation. This significantly increases the transfer of oxygen to the bioreactor biomass, where it is efficiently utilised. This then commensurately intensifies the biological process. As such, an MABR competes with conventional enhanced oxygenation processes - those employing a pure oxygen source rather than air - used in some wastewater treatment applications. The key factors affecting the choice are likely to be the biochemical transformations required and cost.
Enhanced oxygenation
Enhanced oxygenation in biological treatment is an has conventionally been based on pure or enriched oxygen systems. These systems have been implemented in conventional activated sludge (CAS) plants since the late 1960s, predominantly treating industrial effluents of high organic and, possibly, KN (Kjeldahl nitrogen) loads.
Pure oxygen or enriched oxygen aeration (EOA) greatly increases the efficiency of oxygen transfer and utilisation over conventional aeration using air. The transport of molecular oxygen from an air bubble to an individual heterotrophic micro-organism cell is actually a seven-step process, with the liquid phase oxygen transfer normally representing the slowest step. The use of EOA increases the rate if this step by 2-3 times.
The individual steps comprise (see below):
- Transfer from the interior of the bubble to the gas–liquid interface
- Movement across the gas–liquid interface
- Diffusion through the relatively stagnant liquid film surrounding the bubble
- Transport through the bulk liquid
- Diffusion through the relatively stagnant liquid film surrounding the cells
- Movement across the liquid-cell interface
- Diffusion through the floc solid to the individual cell, for cells bond in a floc, clump or solid particle (for individual cells, this step does not exist)
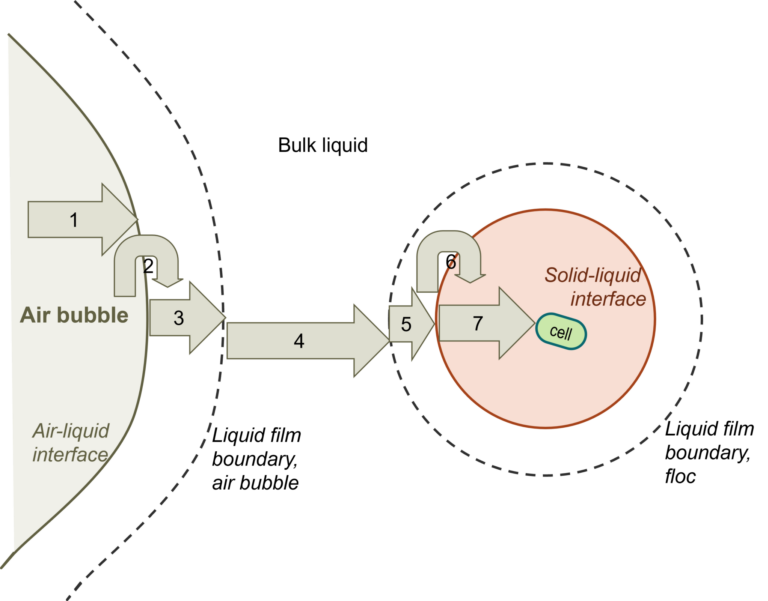
The use of EOA in place of air incurs a financial penalty associated with the supply of oxygen itself. Oxygen can either be delivered from the supplier in bulk and then stored for use, or be generated on site. On-site oxygen generators can produce a 93-95% oxygen-enriched air source, whereas a supplier can provide bulk oxygen at up to 99.99% purity. For biological treatment applications, the lower purity source is sufficient. Under such circumstances, on-site generation is normally more economical and requires less of the infrastructure associated with storage of large volumes of a hazardous material.
The advantages offered by an oxygen-enriched supply are:
- Increased capacity. The primary advantage of an increased rate of oxygen mass transfer is the increase in capacity of the existing plant by providing more rapid treatment at high mixed liquor suspended solids (MLSS) concentrations. This then may obviate any required expansion of the plant capacity by conventional means (i.e. additional infrastructure in the form of tankage, blowers, etc).
- Decreased aeration energy. Since the volume flow of gas is smaller than for air the energy demand for delivering the gas is correspondingly lower.
- Compact aerators. The reduced volume flow of gas also means that only around one third of the aerators are needed compared to the conventional process.
- Tolerance to fluctuating loads. A stable treated water quality can be attained regardless of the strength of the influent, since the oxygenation rate can be tuned to the incoming organic load.
- Tolerance to temperature changes. The decrease in gas solubility at the seasonally higher temperatures does not impose as great a constraint as for it does for conventional aerated systems.
- Tolerance to high MLSS concentrations. Oxygen mass transfer is less constrained by the solids concentration than for conventional aeration, for which the alpha factor decreases either linearly or exponentially with suspended solids concentration.
- Large and stable flocs. The flocs produced tend to be more settlable – with a much reduced risk of bulking from filamentous bacteria - and the sludge generated more dewaterable than that produced by conventional aeration.
- Reduced foam formation. Foam is formed when air bubbles become trapped in the mixed liquor due to its surfactant activity. Foaming, which leads to the loss of active biomass, is less likely to form in the absence of such air bubbles.
- Reduced/no venting. Since the delivered oxygen is almost quantitatively used by the process biology or else dissolved in the wastewater, there is little offgas generated. This means the aeration tanks can be closed to prevent the release of odours or volatile organic carbon which would otherwise be stripped from solution.
Whilst the above advantages can mitigate in favour of implementing an oxygen-enriched air supply for more challenging industrial effluents and where possible constraints apply on site, these tend to be niche applications. In most cases where loads are low to moderate, including almost all municipal wastewater applications, EOA is unlikely to be the most economical choice - though may still be applicable to supplement the existing aeration during periods of high loads.
MABRs
Although MABRs have only been commercialised since around 2015, the process was originally studied in the 1990s at the University of Minnesota in the US and Cranfield University in the UK (Pankhania et al, 1994; Brindle et al, 1998, 1999). The term ‘MABR’ was first introduced by Mike Semmens (Univ. Minnesota). It was originally based on a pure oxygen-fed technology and attracted the interest of gas suppliers like Air Products.
MABRs provide a means of delivering pure oxygen, or an oxygen-enriched air supply, to a biological process with extremely high associated oxygen mass transfer and utilisation. MABRs work by replacing the conventional fine bubble diffuser with a gas-permeable membrane which is selective for oxygen over nitrogen. In doing so the oxygen in the air, or from a pure oxygen source, is introduced in the molecular, or ‘bubbleless’ form.
The use of a membrane to selectively pass oxygen-enriched air directly into an attached biofilm has been shown to increase the oxygen transfer efficiency (OTE) from an assumed value of around 10% for a conventional fine bubble diffuser to as much as 40% (Houweling et al, 2017). FBDAs have been reported as achieving a standard SOTE of 8.5-10% per m aerator depth in an exhaustive review of practical measurements (Behnisch et al, 2020). However, actual OTE values which refer to activated sludge at moderate to high MLSS concentrations are likely to be much lower, particularly if the aerator is also fouled from extended use. Recent work at bench scale using air, rather than pure oxygen, indicated a reduction of up to 85% in process aeration energy compared with conventional fine bubble diffusion (Castrillo et al, 2019).
This leads to highly efficient transfer of oxygen into the solution, since the oxygen is no longer limited by diffusion from the inside of the air or gas bubble to the gas bubble surface and then across the surface to the surrounding water (Steps 2-3 above).
While the membrane provides greatly increased aeration efficiency, and commensurately reduced aeration energy costs, the process incurs a significantly higher cost for the membrane compared to a conventional FBDA. There is also a loss of mixing provided by the air bubbles introduced by the FBDA. Also, as with conventional MBR membranes, the membrane channels can clog as a result of excessive biofilm growth on the membrane surface. The biofilm thickness is normally controlled to below 1 mm by applying periodic air scouring.
The MABR still has a mixed liquor of suspended particles, as with other fixed film processes such the moving bed bioreactor (MBBR), but at lower concentrations than the MBR. Biological treatment is thus achieved both by the biofilm and by the suspended flocs.
This MABR process has been commercially developed and implemented at
full scale since around 2015. Examples of commercial technologies include:
HF: Oxymem (Du Pont, US), Zeelung (Veolia, France)
SW: Fluence (Israel).