The material question − choosing MBR membrane materials

Simon Judd has over 35 years’ post-doctorate experience in all aspects of water and wastewater treatment technology, both in academic and industrial R&D. He has (co-)authored six book titles and over 200 peer-reviewed publications in water and wastewater treatment.
What’s the best membrane material for MBRs? Not being a polymer chemist or materials scientist, it’s one of the many topics I’m able to discuss only from a position of some ignorance. However, it’s one which is reasonably well informed by looking at the range of the products commercialised.
If you consider all the products conveniently listed somewhere (like a book, let’s say ‘Industrial MBRs’) and use that as a basis for measuring the number of products based on each material, it turns out that more than half of the 80 products represented in that book are PVDF (polyvinylidene difluoride).
If you then consider only the polymeric products − so the four ceramic products commercialised at that time are excluded − then the proportion increases to almost two thirds. Of the remaining polymeric products, around 15% are PES (polyethylsulphone) and 10% polyolefinic (either polyethylene or polypropylene), with a couple of PTFE (polytetrafluoroethane) membranes for good measure.
Moreover, the PVDF material has been used for a significant number of products in all three of the configurations (flat sheet, hollow fibre and multitube), whereas the use of PES appears to be limited to the flat sheets and multitubes.
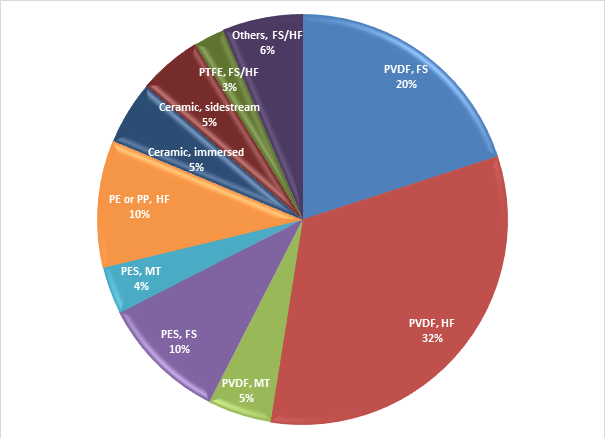
However, that was 3−4 years ago. Just taking a very quick look at some of the products that have been introduced since then (using as a source those that have found their way into The MBR Site membrane products directory), nearly all of them seem to be PVDF-based. So, the inevitable conclusion is that PVDF is by some distance currently the most favoured membrane material for MBRs. This also seems to be the case for other microfiltration/ultrafiltration applications such as raw water filtration for potable water production.
So, why PVDF?
On the face of it, it doesn’t make much sense. PVDF is highly hydrophobic and as such will naturally be fouled by the characteristically hydrophobic organic matter in the mixed liquor.
One of the advantages offered by the ceramic materials is that they are naturally hydrophilic, although a tad more expensive than the polymers. However, the choice of PVDF (or any of the other polymers) is not actually governed by its innate fouling propensity since the material can be made hydrophilic by ‘wetting out’ (forcing the water into the pores by using a hydrophilic gel coating) or through hydrophilic pore formers.
And at this point, due deference should be given to m’colleague Dr Peter Aerts, the Chief Technical Officer of Bluefoot Membranes and formerly (since the turn of the Millennium, indeed) holder of various research positions within DOW Water and Process Solutions. Peter’s view is:
‘The main reason why PVDF is used is because of its superior mechanical properties, and importantly PVDF has significantly higher elongation at break than PES. As a result, it is an excellent polymer to be used in the outside-in (hollow fibre) configuration with air scour that causes the PVDF fibres to flex and stretch. PVDF has a lower pore density than PES, but the outside-in configuration compensates for that to a large degree. Additionally, the robust chemical resistance enables frequent chemical cleaning regimes that are typical and necessary for good MBR operation.’
So, hydrophobicity be damned, it’s the mechanical properties that count.