The ZeeLung MABR technology: the story so far
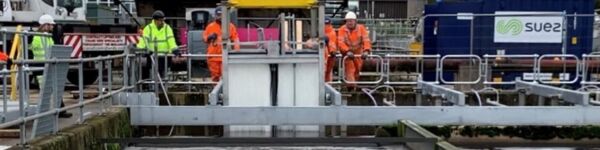
Jeff Peeters, Senior Product Manager ([email protected]), and
Gabriel Kicsi, Senior R&D Manager ([email protected])
SUEZ Water Technologies & Solutions
Find out more about the ZeeLung MABR on the Suez Water Technologies & Solutions website
1. The MABR technology: the fundamentals
The membrane-aerated biofilm reactor (MABR) is, pretty much, exactly as the name suggests. It is a fixed film process where the biofilm is fed with oxygen via the membrane on which the biofilm sits. So, it is a version of a fixed film process, rather than a suspended growth one (as with the MBR).
There are two aspects of this configuration responsible for key treatment benefits:
- 1. the delivery of the oxygen in the molecular (or 'bubble-less') form directly into the biofilm means that the oxygen transfer efficiency (OTE) is very high, and
- 2. the oxygen flows into the biofilm (from the membrane or 'lumen' side) in the opposite direction to the ammonia, which diffuses into the biofilm from the bulk liquid (Fig. 1).
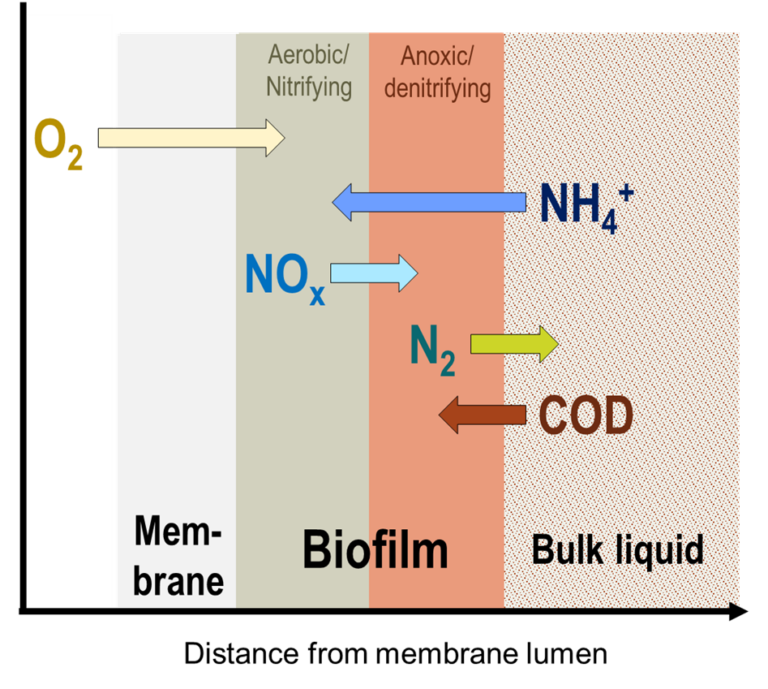
The use of a membrane to deliver molecular (or 'bubble-less') oxygen directly into the biofilm (point #1) is four times more energy-efficient than the use of conventional fine bubble diffusers (FBDs) (Peeters and Natvik, 2021). With FBDs, most of the oxygen (as much as 90%) introduced into the biological process tank escapes the system unused. Given that generating fine air bubbles is a relatively energy-intensive process, it follows that there is a greater loss of energy from oxygenation by FBD than by an MABR.
Aeration is also needed to provide mixing and scouring of the MABR cassette. For the ZeeLung MABR technology, this air is provided by the residual (or 'exhaust') gas from the oxygenation (Fig. 2) (Long et al, 2020). For conventional FBD, the fine air bubbles also provide agitation of the mixed liquor, so a small amount of additional energy is needed for mechanical mixing in an MABR. Even so, the total saving in energy from shifting from an FBD system to membrane aeration is significant – estimated to be 30–40% for full-scale BNR upgrade based on existing installations (Frensch et al, 2019; Peeters and Natvik, 2021).
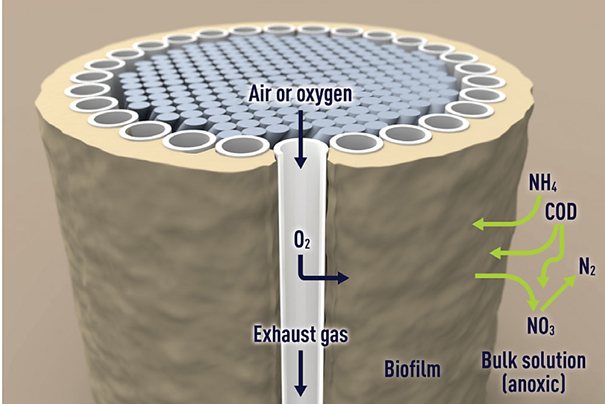
The promotion of the growth of nitrifiers in the aerobic region (point #2) provides a second key advantage over suspended growth and conventional biofilm processes. It effectively increases the volume concentration of these bacteria by creating favorable conditions for their growth. In this respect, an MABR has more in common with other biological fixed-film media processes, like the integrated fixed-film activated sludge process (IFAS) or the moving bed bioreactor (MBBR).
However, unlike other fixed film processes, the membrane both increases the overall energy efficiency of oxygen delivery to the biofilm and also adds an extra element of:
- 1. process control with respect to the rate of oxygen transfer into the biofilm, which increases the oxygen transfer efficiency to around 3.6–4.0 kgO2 per kWh, and
- 2. intensification through concentration of the active microbiology (or biomass), and the nitrifiers in particular, in the biofilm, which then permits more effective nitrification.
Since the biomass is concentrated and attached to the membrane, the reactor volume can be commensurately reduced for a given suspended solids concentration without compromising biological performance.
The process also offers greater robustness to high C:N ratios, attributable to the counter-diffusional nature of the biofilm. To reach the O2, a molecule of ammonia or COD must first diffuse through the biofilm from the opposite side (Fig. 1). Since the ammonia molecule is smaller than the predominantly macromolecular organic matter making up the COD, it diffuses more rapidly through the anoxic layer to the aerobic region. As a result, the inner biofilm is enriched in nitrifiers. This distinguishes the MABR biochemistry from the co-diffusional biofilms associated with a conventional fixed-film process.
As a direct result of this biofilm structure, simultaneous nitrification and denitrification is provided within the dual-layer biofilm. By installing the membrane cassettes in the anoxic zone of an activated sludge system (Fig. 3), ammonia can be nitrified under aerobic conditions in the biofilm and nitrate reduced to nitrogen gas under the anoxic conditions of the suspended biomass in the bulk of the anoxic tank. The reduces the requirement for recycle pumping to achieve total nitrogen (TN) removal.
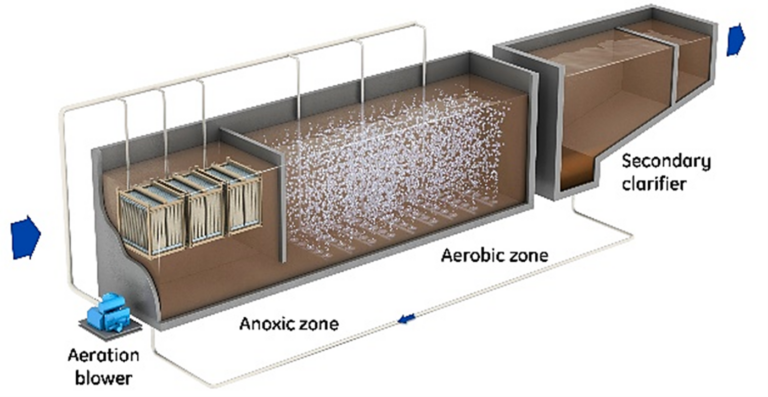
Finally, it appears that MABRs, in common with other fixed film processes, can provide stable performance over a range of temperatures. The technology has been shown to be robust to low temperature operating conditions, where nitrification is often inhibited in CAS systems: a decrease in temperature from 20 to 11°C did not impact on the nitrification rate, according to the outcomes of an extended pilot trial (Long et al, 2020).
2. The MABR product
There are currently three commercial MABR products: the ZeeLung, offered by SUEZ, Oxymem, a Du Pont brand, and Fluence. The ZeeLung product is a supported hollow fibre (HF) membrane configuration in which multiple membrane filaments are oriented around a structural support (Figs. 2 and 4) to form a robust cord. Multiple cords are potted into a top and bottom header to create a module. A series of modules are installed in a stainless-steel cassette, which forms the modular building block for the MABR system.
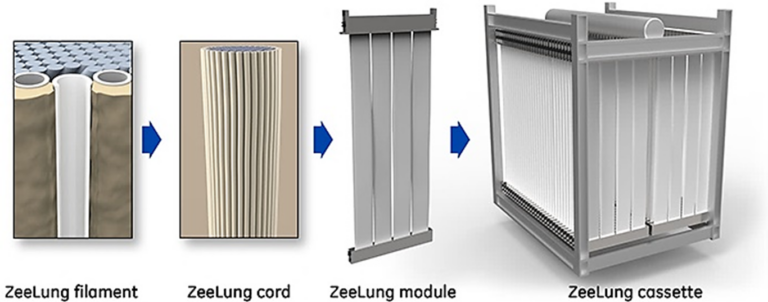
Low-pressure air is delivered to the cassette using typical process aeration blowers. The air is distributed down the length of the ZeeLung
filament lumens where oxygen is transferred through the media to satisfy the oxygen demand in the biofilm. The remaining 'exhaust' air is collected and used for mixing via a coarse bubble aeration grid at the base which is integral to the cassette. This mixing provides sufficient energy to renew substrate at the biofilm surface and slough-off excess biomass to control the biofilm thickness to within 200 to 500 µm (Long et al, 2020).
The ZeeLung is a typical modular system where the modules, 844 x 52 x 2198 mm high, are fitted into a cassette. Each module provides an effective membrane area of 40 m2. The membrane area per module footprint is then 911 m2 membrane per m2 floor area.
3. The principal applications
The process intensification and enhanced efficiency elements make the technology well suited to upgrading or expanding existing activated sludge-based wastewater treatment works (WwTWs) which are subject to:
- 1. loads above their design values and/or
- 2. tighter discharge permits, especially with respect to nutrients.
The increased biomass levels coupled with a decreased suspended solids retention time permits a greater treatment capacity for the same tank volume. This means that the plant capacity (i.e. the load), and/or the nutrient removal, can be increased without requiring additional tankage.
Currently, there are 17 commercial applications of the SUEZ ZeeLung technology in operation, construction or design globally. The first landmark full-scale installation was at the Yorkville-Bristol Sanitary District, IL, in 2017 (See 4.1).
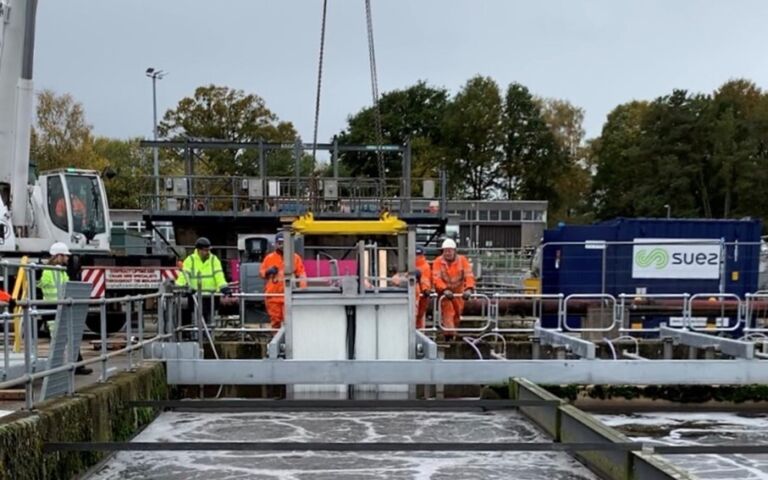
4. Case studies
4.1 Yorkville-Bristol Sanitary District, IL
The 13.7 MLD capacity MABR at the Yorkville-Bristol Sanitary District (YBSD) in Illinois, commissioned in late 2017, represents the world’s largest MABR installation in terms of hydraulic treatment capacity (Underwood et al, 2019). The plant serves a population of 18,500 and discharges to the Fox River, an impaired water body.
Prior to the upgrade the facility was a single-stage nitrifying CAS system. Population growth and the arrival of new industrial contributions were anticipated to result in the facility exceeding its rated organic capacity. At the same time, Yorkville had to comply with a new total phosphorus limit of 1 mg/L. This situation required the plant to be upgraded to increase organic treatment capacity and implement phosphorus removal.
The existing site is footprint constrained; a conventional upgrade would require construction of a separate treatment plant on adjacent property. Yorkville sought a retrofit solution that would minimize capital expenditure and avoid significant civil modifications to the facility, while accelerating the implementation schedule by avoiding the time required to permit and construct a new plant.
The ZeeLung technology in combination with enhanced biological phosphorus removal (EBPR) was chosen to upgrade the plant, motivated principally by:
- the 45% increase in organic treatment capacity within the existing bioreactor volume
- a 75% capital cost saving compared to building a new conventional plant
- rapid implementation
- the synergy between ZeeLung and EBPR, and
- no net increase in energy consumption.
The simultaneous nitrification and denitrification provided by the MABR technology reduces the nitrate load to the EBPR anaerobic reactor. The reconfiguration of the plant to encompass MABR and EBPR demanded no additional tankage (Fig. 6). The increased capacity provided and tighter effluent limit achieved does not come at the expense of increased energy demand.

The upgrade employs 12 ZeeLung cassettes per tank, providing 23,000 m2 of membrane area and requiring 102 Nm3/h of process air at a feed pressure of 345 to 414 mbar(g). The ZeeLung blowers and other auxiliary equipment (compressor and dryer for pneumatic valves, variable frequency drives for the blowers and the jet mixing pump, programmable logic controller and human machine interface) are housed in a 24.6 m2 dedicated building. Thus far only one of the two trains (Tanks 1−5) has been upgraded, with upgrade of the second train planned in the future.
The ZeeLung upgrade has been in operation since its installation, reliably delivering increased nutrient removal and energy savings.
4.2 Hespeler, Cambridge, Ontario
The 9.32 MLD Hespeler WwTP components included a raw sewage pumping station, grit channels, extended aeration (EA), chlorination and de-chlorination, and sludge storage. The MABR option for secondary treatment was evaluated to ‘future-proof’ the site and meet imminent ammonia effluent limits, having upgraded with new screening/grit removal and secondary treatment, and converting existing sludge storage to aerobic digestion (Peeters and Natvik, 2021).
The implementation of MABR at this site entails:
- the selection of 2-mm fine screens, in the absence of primary clarification at the site
- reserving sufficient space for MABR-related tanks and equipment, and
- providing sufficient hydraulic head and interconnections to allow gravity flow.
Modelling of aeration and energy demand for an EA and MABR-based upgrade revealed the MABR to be ~30% lower in energy demand (Table 1). Determination of capital costs indicated showed the MABR design to cost $6m, compared with $11m for the EA. Similar MABR construction cost savings are expected for expansion beyond the current rated 9.32 MLD capacity, relating mainly to the reduced process footprint compared to EA expansion.
Parameter | EA | MABR |
---|---|---|
Average flow, m3/d | 9320 | 9320 |
Plant loads, mg/L | ||
Average cBOD5 | 206 | 206 |
Average TKN | 42 | 42 |
Process biology oxygen demand, kgO2/d | ||
MABR AOR | − | 505 |
Aeration Tank AOR | 2710 | 1910 |
Total AOR | 2710 | 2415 |
Aeration demand, Nm3/h | ||
Airflow for MABR tanks | − | 305 |
Airflow for aeration tanks (ATs) | 4510 | 2935 |
Total AT+MABR Airflow | 4510 | 3240 |
Blower Power, kW | ||
AT Blower Power | 74 | 48 |
MABR Blower Power | − | 5 |
Total AT+MABR Power | 74 | 53 |
Yearly Power use & cost | ||
Annual power use, kWh/y | 648,300 | 464,300 |
Annual power cost @$0.14/kWhr | 91,000 | 65,000 |
Implementation of MABR technology was sanctioned following the securing of funding in November 2019, with the following key design elements:
- inlet valve chamber to allow flow control of MABR bypass of raw sewage and/or return activated sludge
- influent flow splitter box with jet mixing and nozzles extending into blank cassette spaces
- four parallel MABR tanks, each containing nine ZeeLung cassettes and two blank spaces to allow future cassette integration
- hydraulic provision to raise cassettes 600 mm should internal cassette MLSS mixing prove inadequate, and
- on-line instrumentation (flowmeters and analyzers) to facilitate commissioning, research, testing and confirm MABR performance.
The MABR system is currently under construction and will be operational in 2022.
5. Conclusions
The primary value proposition of the MABR technology is the ability to provide process intensification while also reducing energy consumption. Additional advantages are the simplicity of the implementation of the solution compared to the civil works required for a conventional activated sludge upgrade and improved process resilience from the attached growth biofilm. Direct delivery of oxygen through the membrane and into the biofilm permits enhanced oxygen transfer and usage for the aerobic biological processes. At the same time, it also allows a measure of control over the biofilm microbiology to the point where nitrification within the membrane-attached biofilm can be conducted even within the bulk anoxic conditions of the denitrification tank. Performance is largely unaffected both by low temperatures and high loads.
The ultimate demonstration of biochemical process control is in the most recent pilot-scale demonstration of the technology for a new application – the 'partial-nitritation/anammox' process biochemistry, whereby further energy savings are made by obviating the complete oxidation of ammonia to nitrate (nitrification). This technology, named ZeeNAMMOX, relies on maintaining a consortium of Anammox (AMX) microorganisms to achieve deammonification (biochemical reduction of nitrite and ammonia to nitrogen gas), demanding precise control of the biofilm oxidative conditions. In the one-year trial, the AMX population took ~200 days to accumulate in the biofilm, from an unseeded bioreactor. The process was maintained by feedback control through monitoring of the gas phase oxygen concentration. Once fully acclimatised oxygen transfer efficiencies above 95% were attained with specific energy consumption values of below 0.3 kWh per kg N−NH3, or <0.4 kWh per kgN removed (Kicsi et al, 2021).
The future of MABR technology looks assured. Its adoption has been somewhat quicker than for MBR technology, where a degree of reticence was originally experienced. There is greater acceptance of membrane-based systems in wastewater treatment, and the value added to the process biology has been clearly demonstrated. Given this attribute, the retrofit market − where the capacity of existing facilities can be expanded and tighter consents met without extensive civils work − appears to be particularly favourable.