Degritting in MBRs − true grit costs
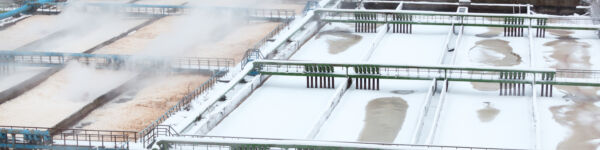
Simon Judd has over 35 years’ post-doctorate experience in all aspects of water and wastewater treatment technology, both in academic and industrial R&D. He has (co-)authored six book titles and over 200 peer-reviewed publications in water and wastewater treatment.
There’s plenty of tales of the impact of poor screening on downstream unit operations generally and on MBRs in particular. While there is very little actual proper research into the performance of screens published in the peer-reviewed literature, there are some useful guidelines produced by practitioners − including one appearing on this very web site (MBR Screening Part 2: Selecting an MBR screen).
Fine screens generate more screenings, which is unlikely to endear them to the operators, but the protection provided by them can save a lot of grief with downstream operations. This is particularly so with the membrane separation technology, where sludging and ragging can play havoc with operation and maintenance (From rags to hitches: clogging by rag reconstitution in MBRs).
So what about the other key preliminary treatment process? As with screening, degritting is (a) an almost ubiquitous unit operation for large municipal wastewater treatment plants, and (b) largely ignored by the academic community as a research topic. Unlike screening, which is pretty hard to model or represent in a laboratory (making it a challenging and expensive proposition for any researcher), degritting performance is governed by the laws of hydraulics and sedimentation. Admittedly, defining settlement of granular particles in intermediate and turbulent flow regimes is a little challenging but that’s why God gave us modellers. The situation is also complicated by the likely existence of composite particles − grit particles coated with fat − where the fat reduces the overall density and apparently makes them less settlable (Judd et al, 2017).
As with anything else in wastewater treatment, and indeed life, the number one question is: how much does it cost?. A degritter is unlikely to be the most expensive item in a wastewater treatment works but it’s a pretty important one: the impact of residual grit can apparently be quite significant.
Possibly the doyen of this field is the charmingly urbane Brian McNamara of the Hampton Roads Sanitation District in Virginia. Brian brightly stated 'grit is my life' when he visited Cranfield a couple of years back, which does rather suggest he should get out more. He was able to regale the assembled throng of UK water industry practitioners with a cornucopia of anecdotal information on the perils of grit. These range from abrasion (predictably enough) to the filling of digesters and aeration lanes, reducing the time between their scheduled maintenance (a fairly costly affair).
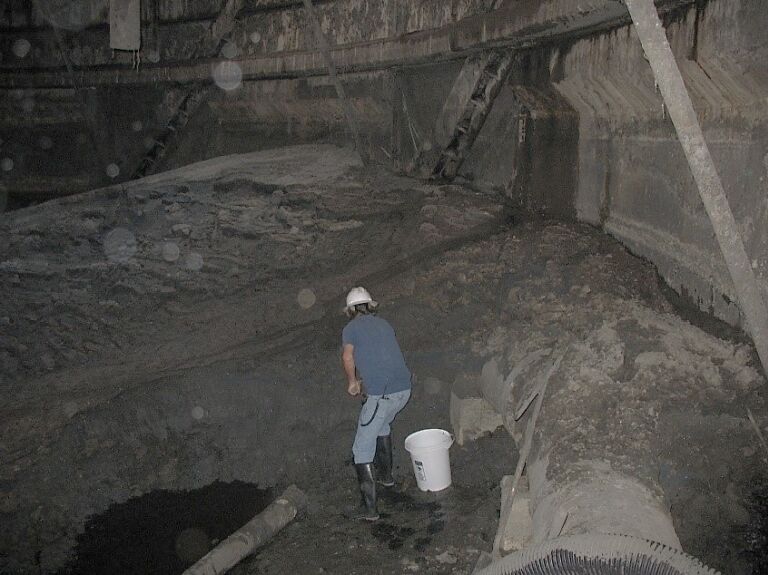
Pooling all available cost data from either side of the Atlantic, it seems that costs attributable to grit breakthrough come to, on average, something in the region of $8.2 per megalitre (ML) water treated (Judd et al, 2017). This figure was based entirely on conventional activated sludge (CAS) processes. Impacts on MBRs specifically are unknown, but some of those sand particles are pretty sharp and it might be expected they would treat a polymeric membrane with a degree of disrespect.
Even at only $8.2/ML for CAS technologies the costs stack up significantly. Considering the investment cost, if upgrading the degritter is assumed to halve the level of residual grit, then for a 25 MLD plant with an asset life of 25 years and an assumed discount rate of 4%, the cost saving would be $0.56m. In other words, spending an extra half million dollars on upgrading the degritter for a new build to ensure the residual grit levels were halved would be an economically viable proposition. One assumes that degritter technology suppliers would be mightily heartened by this news.
There’s plenty that’s been said about the crucial importance of screens upstream of an MBR. This was a key finding from the pioneering pilot trials at Beverwijk conducted by DHV in the late 90s and early noughties (STOWA, 2002).
But spare a thought for the degritters – if only for Brian’s sake.