A complete fabrication – producing membrane modules in Austin, Texas
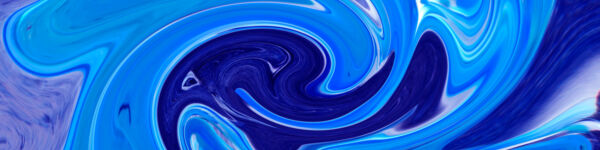
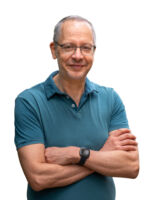
Simon Judd has over 35 years’ post-doctorate experience in all aspects of water and wastewater treatment technology, both in academic and industrial R&D. He has (co-)authored six book titles and over 200 peer-reviewed publications in water and wastewater treatment.
Claire and myself were fortunate enough to be among the visitors to the grand opening of MICRODYN-NADIR’s new US-based MBR membrane manufacturing facility in Austin last week. MICRODYN-NADIR, a membrane manufacturing company headquartered in Wiesbaden, Germany, opened the 27,000-square-foot facility on Thursday 3 May. The automated facility will produce BIO-CEL® modules, and a dedicated section of the building will house engineers from US-based MBR system manufacturer Ovivo.
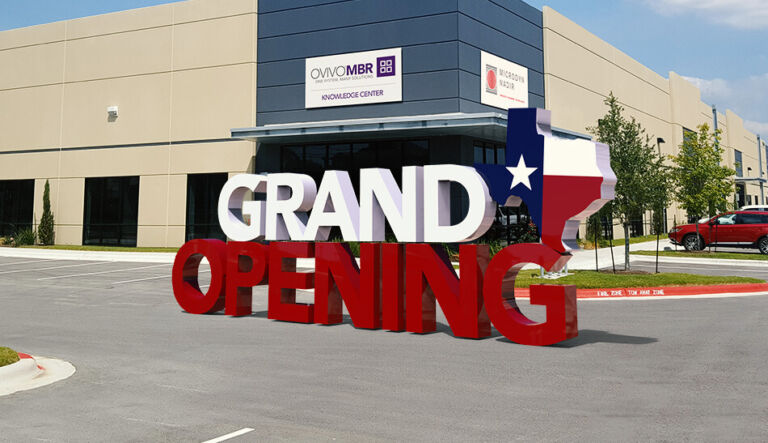
Ovivo have hosted an MBR Operators’ Workshop every two years (formerly yearly) since the mid-noughties, and this time the event was planned to coincide with the formal grand opening ceremony of the fabrication facility. Having sat through the rantings of a sad old academic banging on about clogging and ragging for much of the previous day, the operators were due some respite and were duly impressed by this facility.
As well they might be. While a flat sheet membrane may appear to be a simple enough piece of equipment, automating its construction is anything but. Clearly, the finer points of manufacturing, mechanical and electrical engineering will only ever be lost on someone whose mechanical knowledge extends only as far as pumping sludge (and still struggles with mastering the settings of an Ipad, as others will attest). However, it’s impossible not to marvel at how a sizeable robotic arm is able to cut holes so precisely in a membrane sheet − presumably within a tolerance of a mm or less − where the mounting rods and permeate headers have to be placed. But then again this is a nation responsible for Mercedes and BMW motor cars, not to mention the hamburger, so I suppose it shouldn’t really be too surprising.
One does wonder though, witnessing something so highly automated and efficient, how it is possible to make the product any cheaper. I also had the pleasure of visiting the ZeeWeed manufacturing plant in Hungary a few years back and recall being similarly awestruck. And, to the best of my knowledge, there are manufacturing plants in China producing MBR hollow fibre membranes on a massive scale.
It is well known that the cost of polymeric MBR membranes − both flat sheet and hollow fibre − has fallen considerably since they were first commercialised in the early 1990s and that this can be attributed to the law of supply and demand, leading to mass production and lower costs per unit. Demand for MBR membranes in China in particular is staggeringly high: just look at the list of the world’s largest MBR plants. If manufacturing is now as efficient as it can be, and a quick skim through the products on offer suggests that most suppliers have settled on PVDF as the go-to material, then perhaps the cost of polymeric MBR membrane supply has already bottomed out.
But whether this also applies to ceramic membranes, in which Ovivo coincidentally also has a commercial interest, is less certain. Ceramic membranes are still considered to be niche and yet, as highlighted in a previous blog (see blog: The cost of ceramic membranes for MBRs), the specific cost of the membrane per unit volume of water treated is dependent on both the flux and the membrane life alongside the cost per unit area of material. The figures for the latter currently remain relatively high, but it seems more than likely that this cost would decrease further at higher demand in the same way as it has for polymeric membranes.
But in the meantime, there is evidently a substantial enough commercial opportunity in the US to warrant the bold move of setting up a dedicated manufacturing facility for flat sheet polymeric membranes − and a pretty slick one at that. As far as the MBR market as a whole is concerned, this can only be a good thing: regional manufacturing to feed the local market makes economic sense and presumably permits greater adaptability and responsiveness.
Let’s hope the US appreciates all that good German engineering coming its way. The signs are good − if the success of the hamburger is anything to go by.