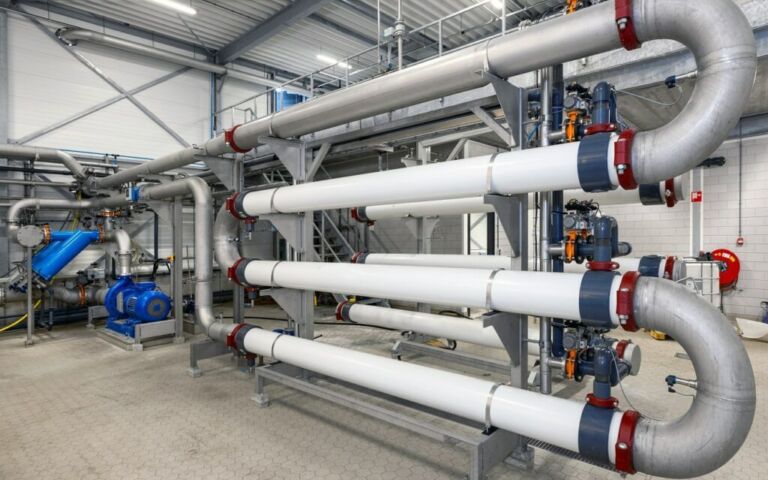
Industrial MBRs − an introduction
Membrane bioreactors have been applied to treat effluent in a number of industrial sectors including food and beverage, petroleum, pharmaceuticals, landfill leachate and ship effluent. MBRs for industrial effluent treatment operate at lower fluxes and longer hydraulic residence than those implemented for municipal wastewaters.